Firmenansichten Werk Piepersberg
Ein Überblick zu den verschiedenen Hallen auf unserem Firmengelände.
Hallen 1 & 2
Entwicklung – Endmontage – Prozessoptimierung
Der reguläre Gestellbau, die Endmontage der Gestelle, ist in der Haupthalle der Firma untergebracht. Dort erfolgt die Zusammenführung der einzelnen Bauteile parallel über zehn gut ausgerüstete Stationen.
Fünf hochmoderne WIG/MIG-Schweißkabinen, die zentral mit Gas versorgt werden, unterstützen die geschulten Fachkräfte beim Zusammenbau der Gestelle. Erst wenn die Qualitätskriterien der so gefertigten Gestelle zu 100 Prozent erfüllt sind, wandern sie in die automatische Beschichtungsanlage. Auffällig ist die großzügige Konzeption der Arbeitsplätze, so haben die Mitarbeiter ausreichend Platz, um sich bei der Endmontage auf die Qualität und Funktion der zu bauenden Gestelle zu konzentrieren. Artimax ist stolz darauf, ein Arbeitskonzept entwickelt zu haben, in dem Prozesse nahtlos ineinander greifen. Auch deshalb ist das Unternehmen laut Arbeitsschutz schon viele Monate unfallfrei.
In einem abgetrennten Teil der Halle gibt es auch ein Materiallager mit komplettem Maschinenpark, nur alles viel kleiner als in der Bauteile-Vorfertigung. Auf meine Frage, was das zu bedeuten habe, bestätigt mir Geschäftsführer Herr Alfred Marx, dass wir uns hier im Forschungs- und Entwicklungsbereich von ARTIMAX befinden. Hier können Änderungen, neue Ideen und unkonventionelle Denkansätze zeitnah in Prototypen umgesetzt werden, welche dann praxisnaheTests durchlaufen.
Im ersten Stockwerk des Hauses befindet sich die Verwaltung des Unternehmens mit Kundenempfang und neuem Konferenzraum. Über ein kürzlich eingeführtes Warenwirtschaftssystem können jetzt alle Vorgänge der Produktion bis zur Auslieferung und Installation beim Kunden digital erfasst werden.

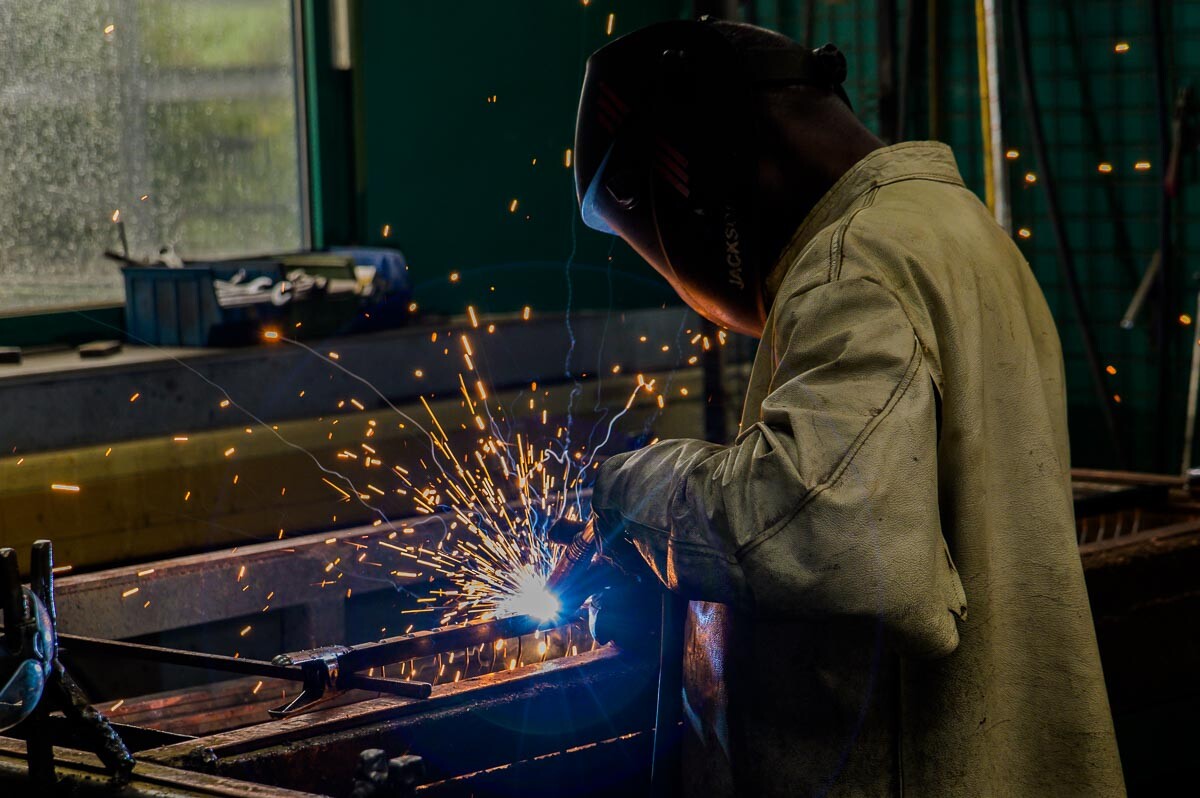
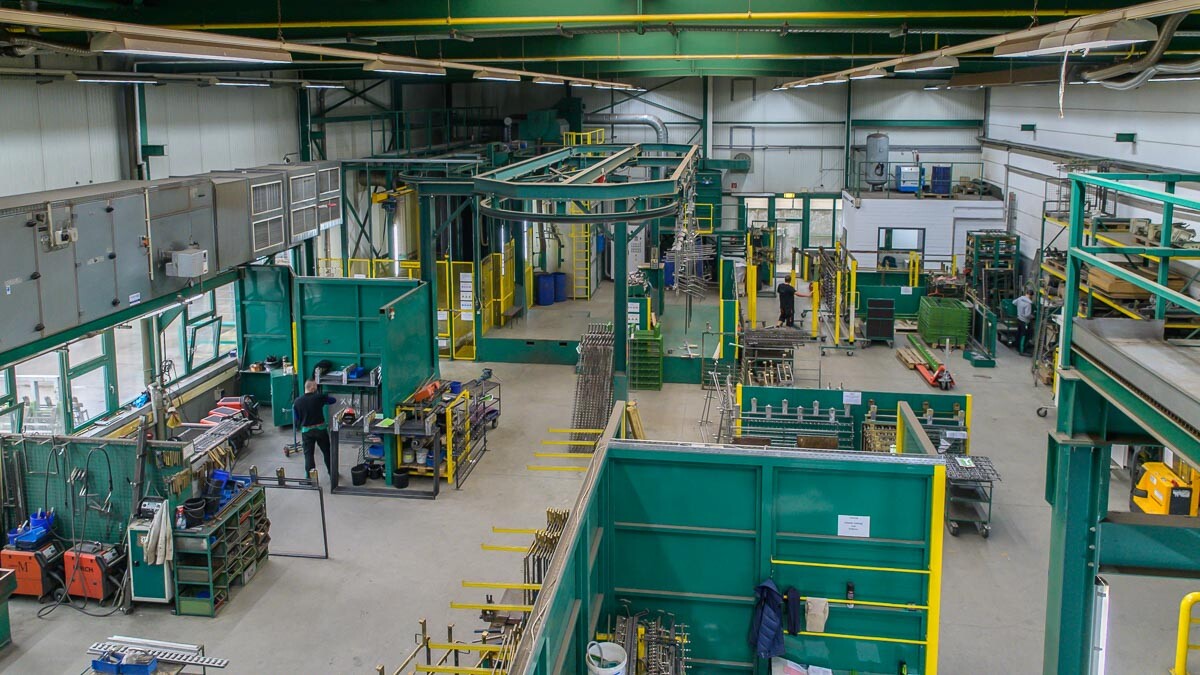
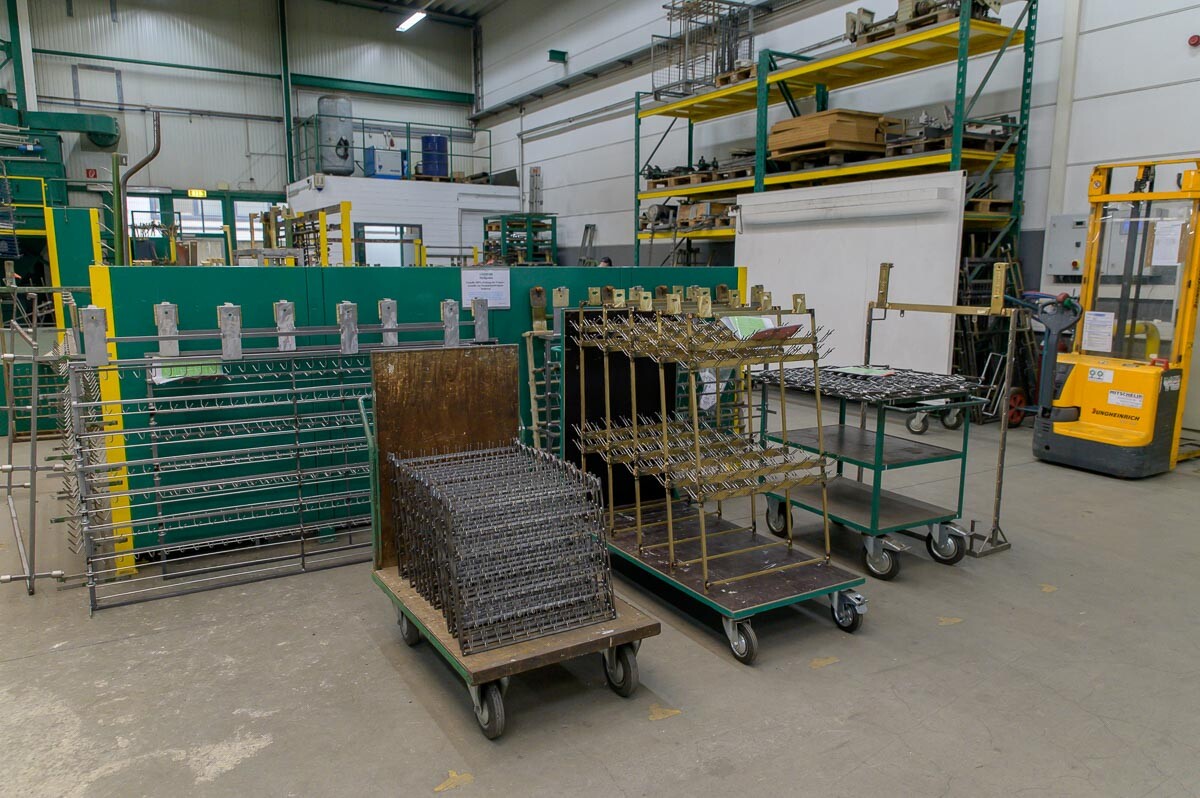
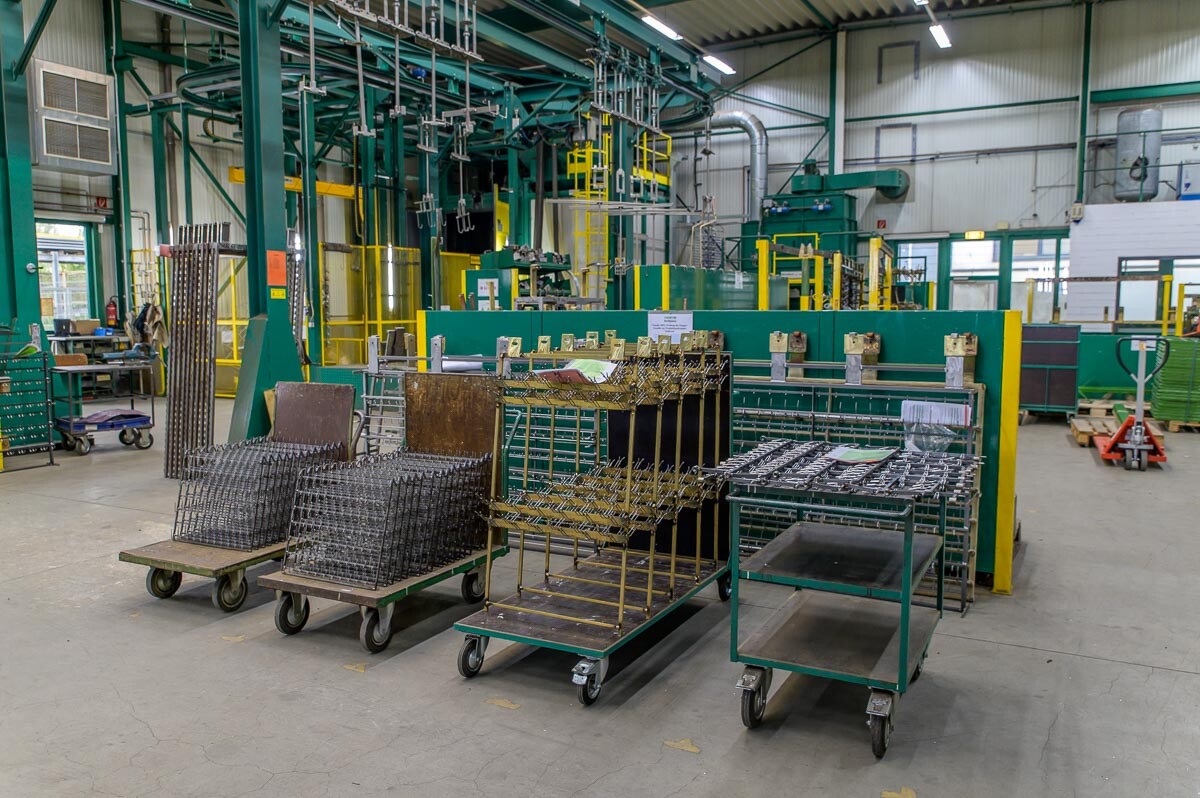
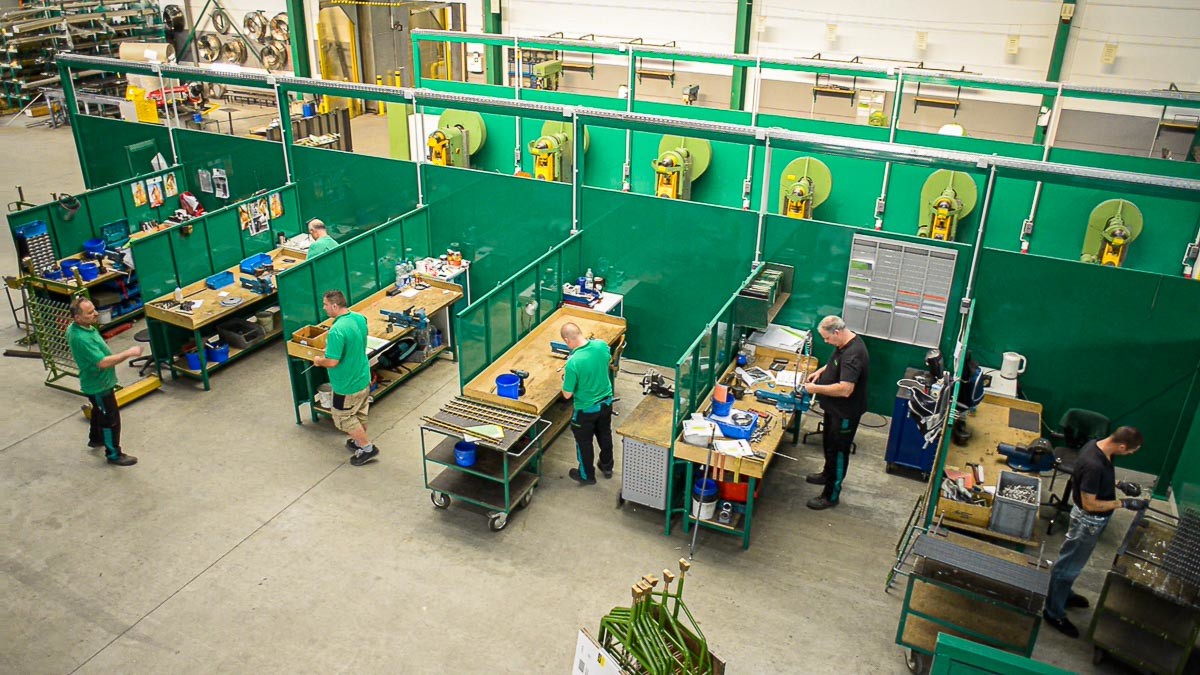
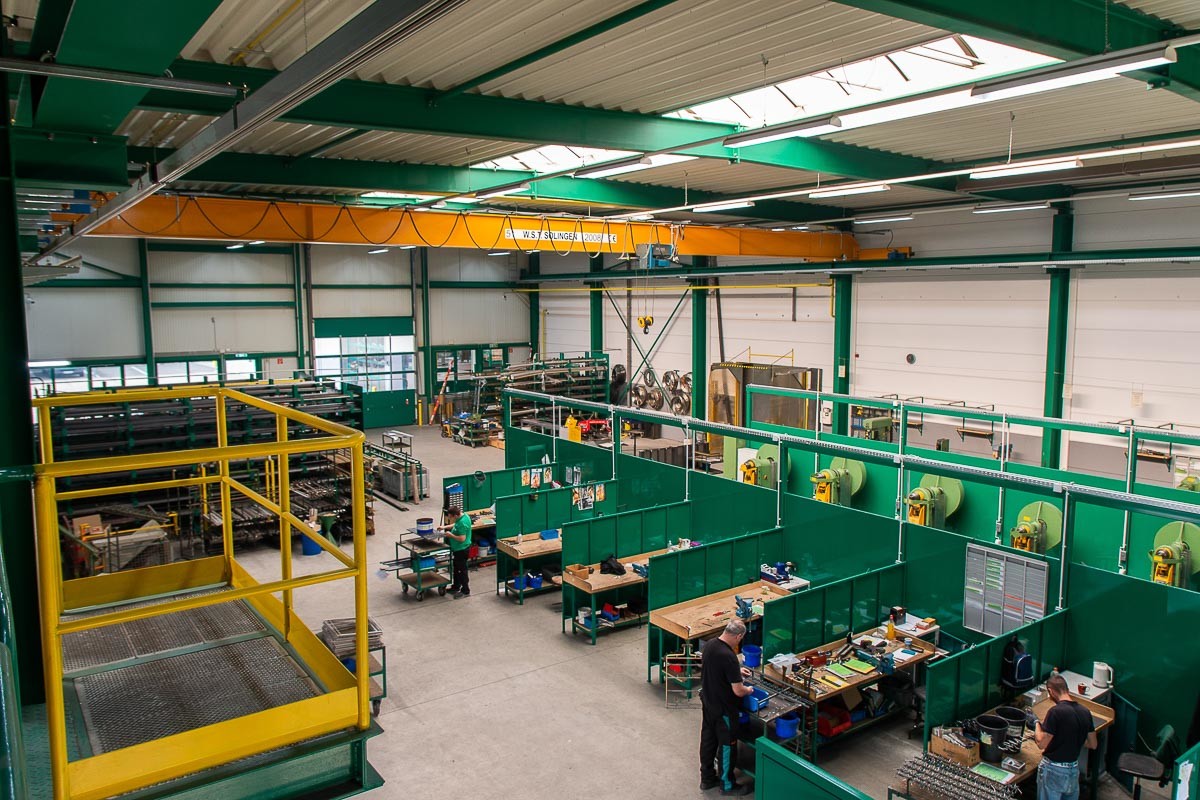
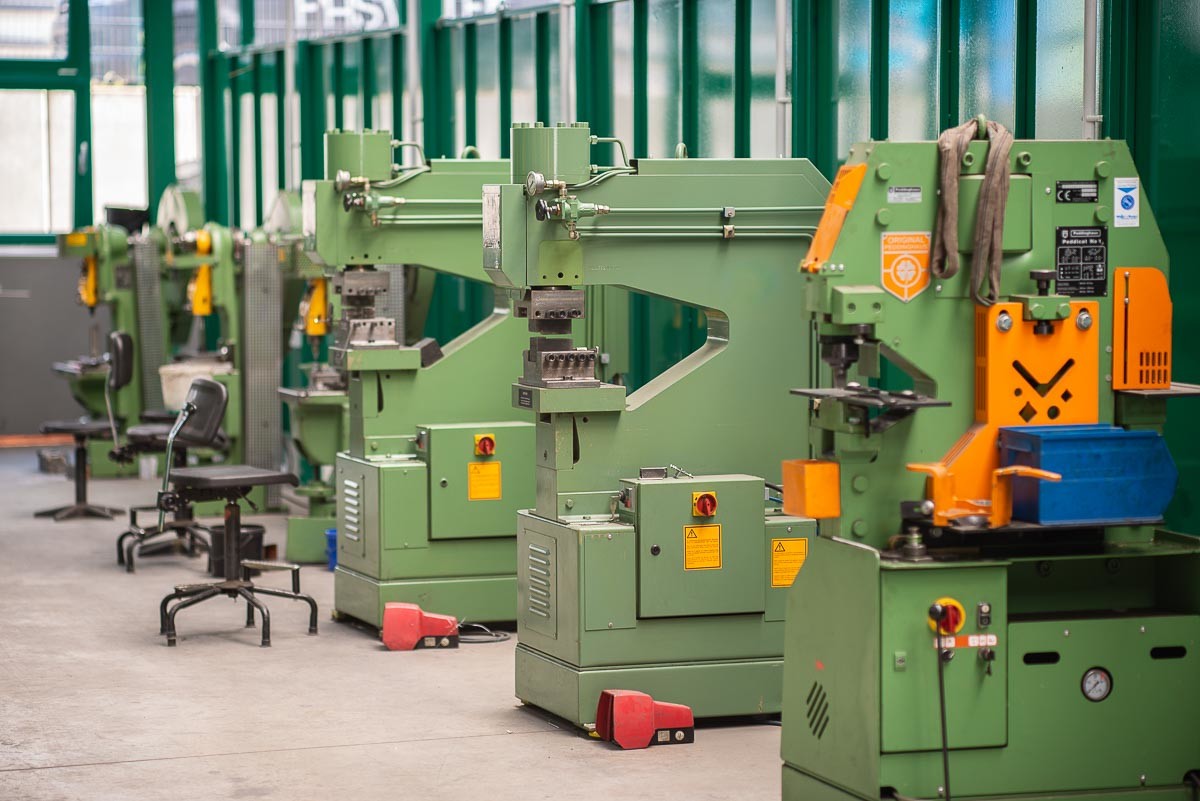
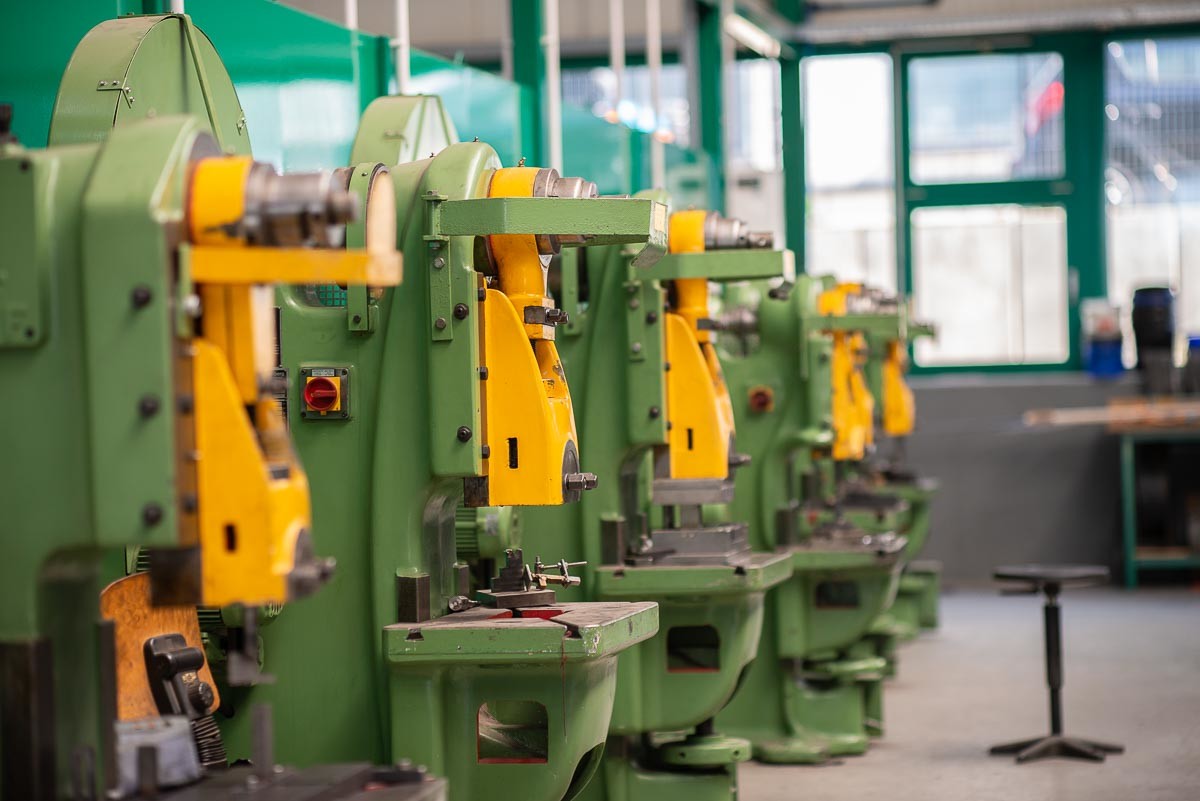
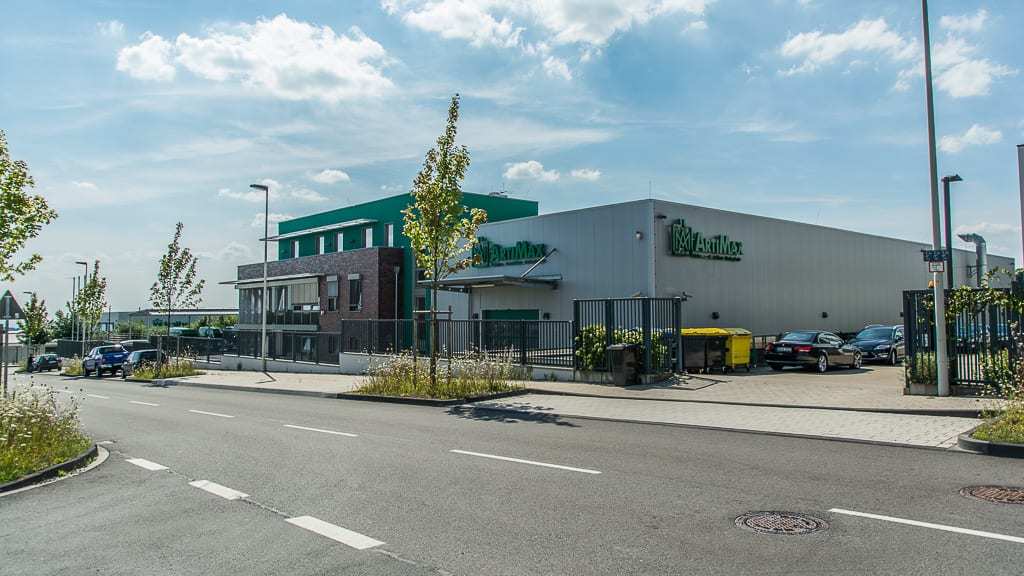
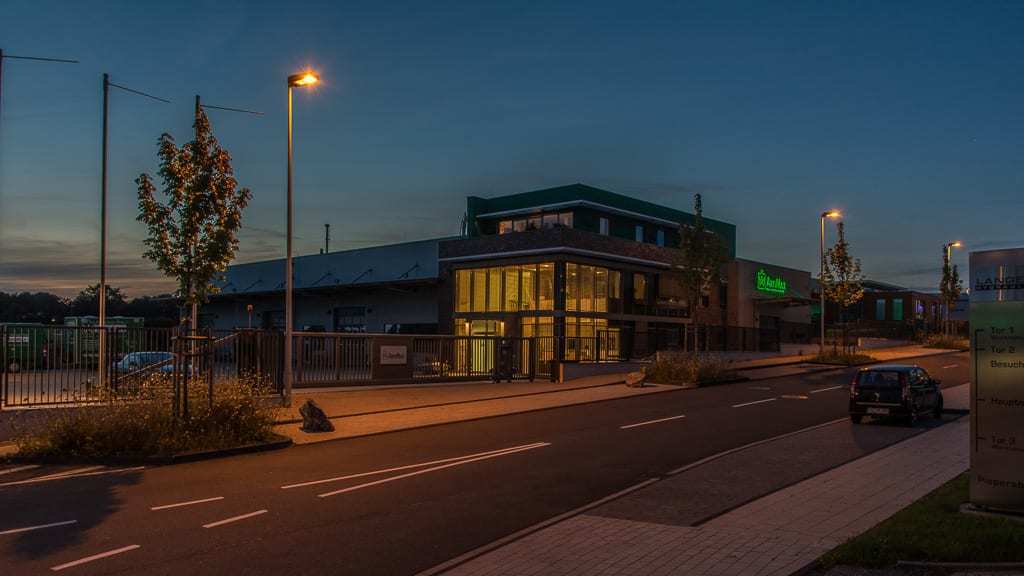
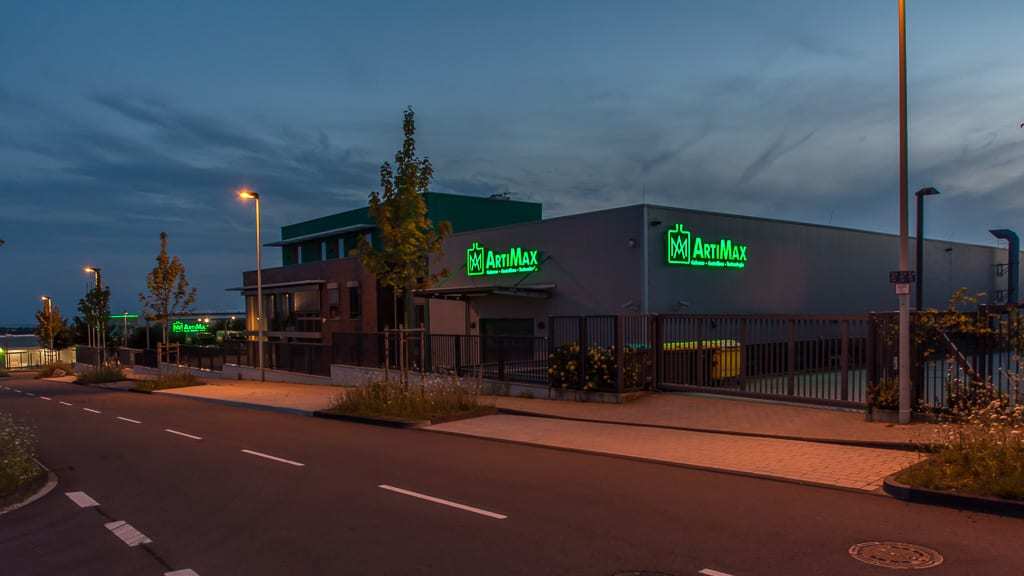
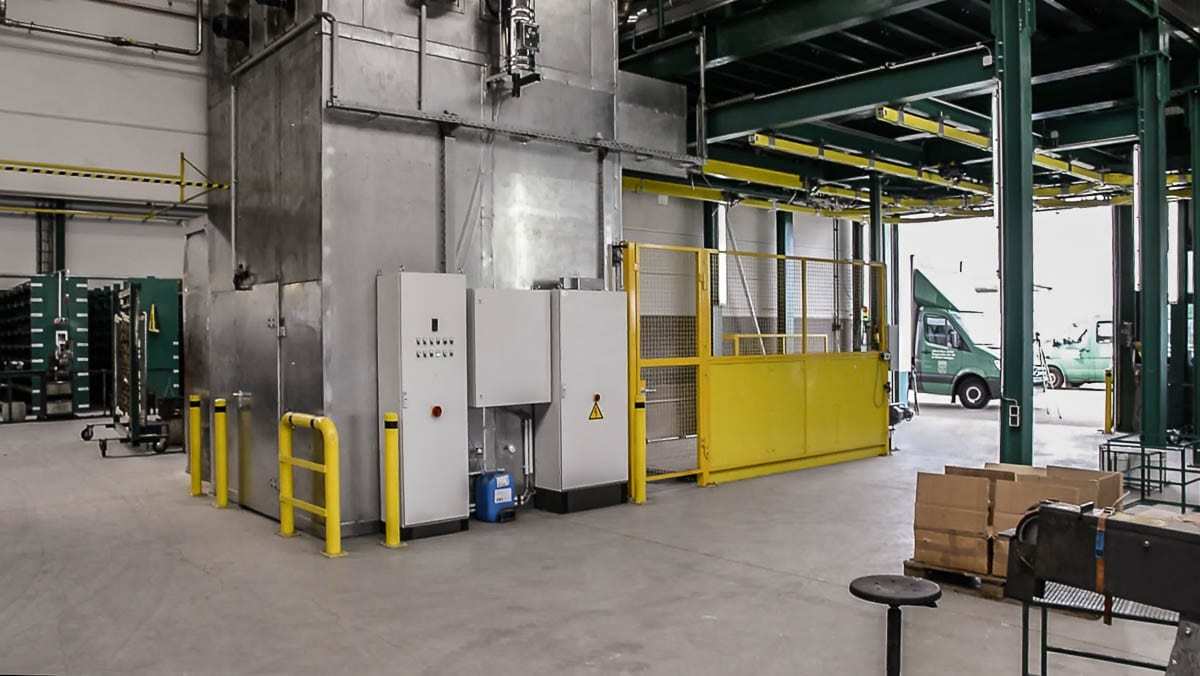
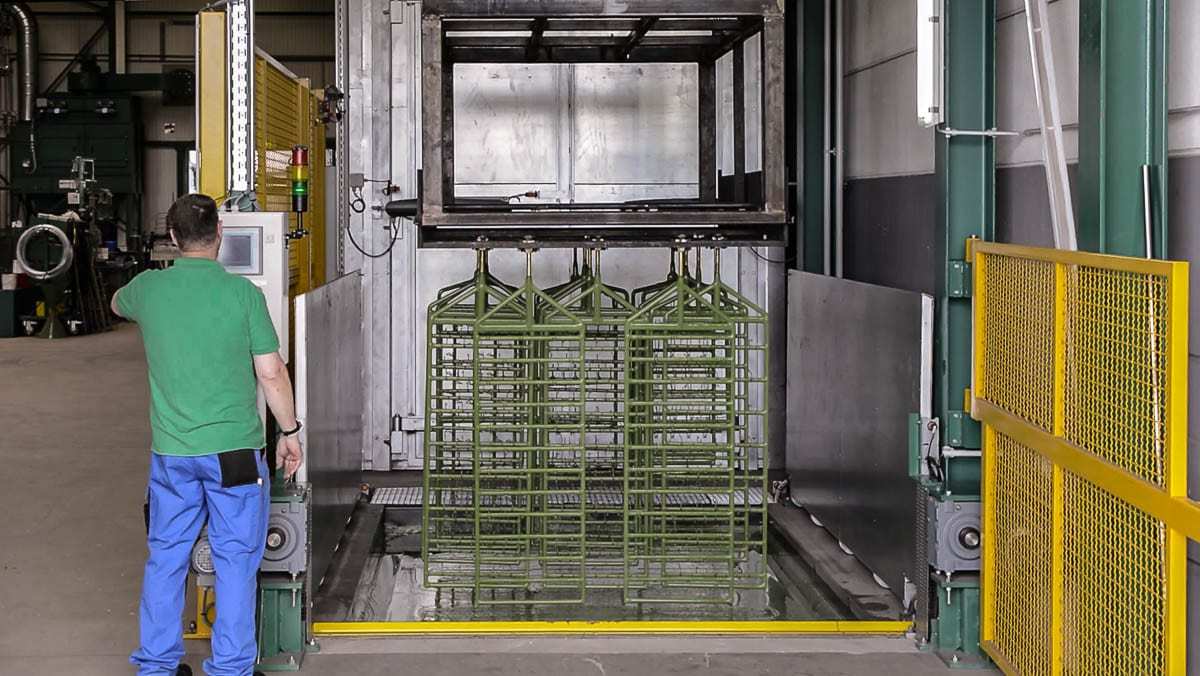
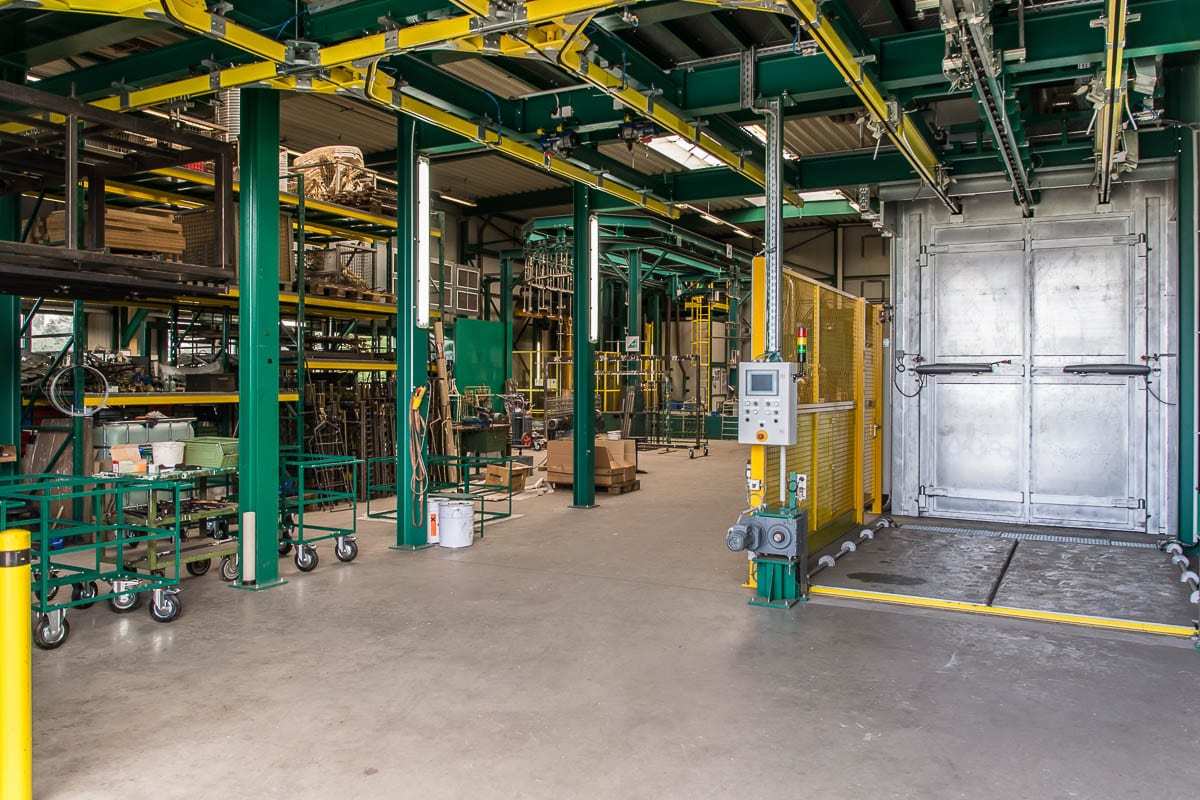

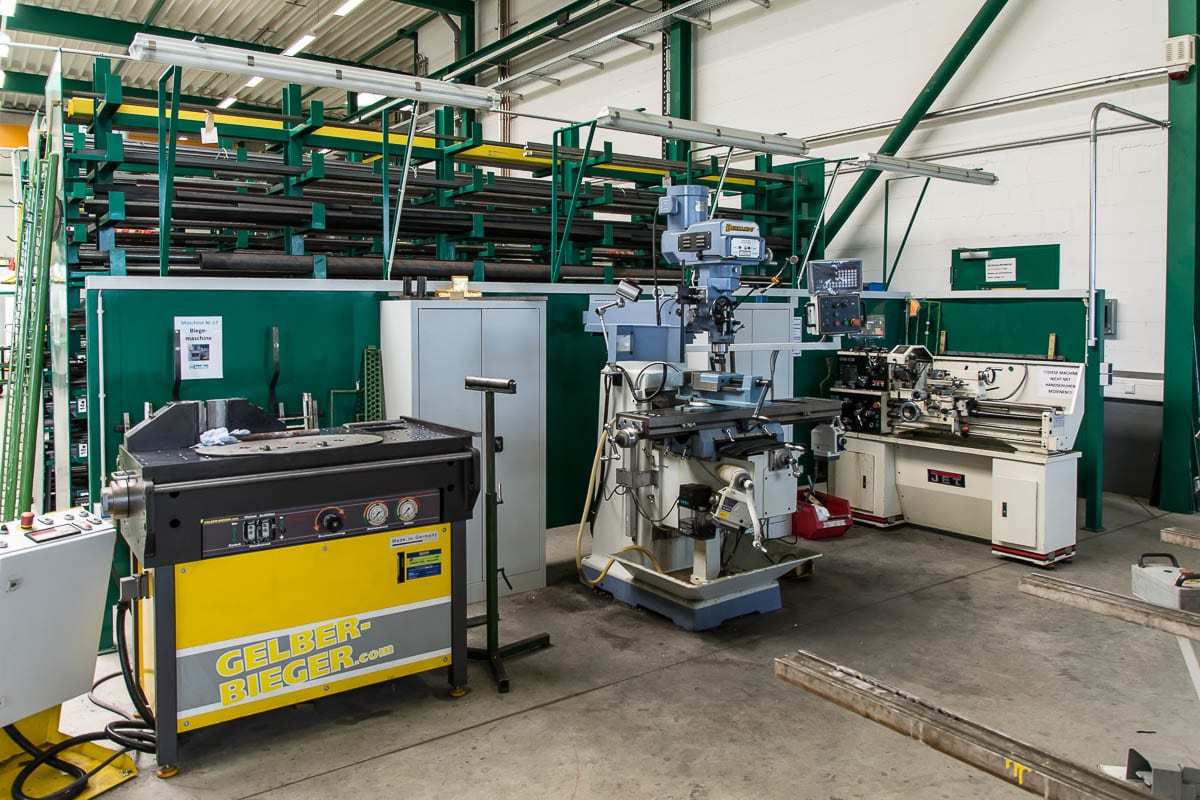
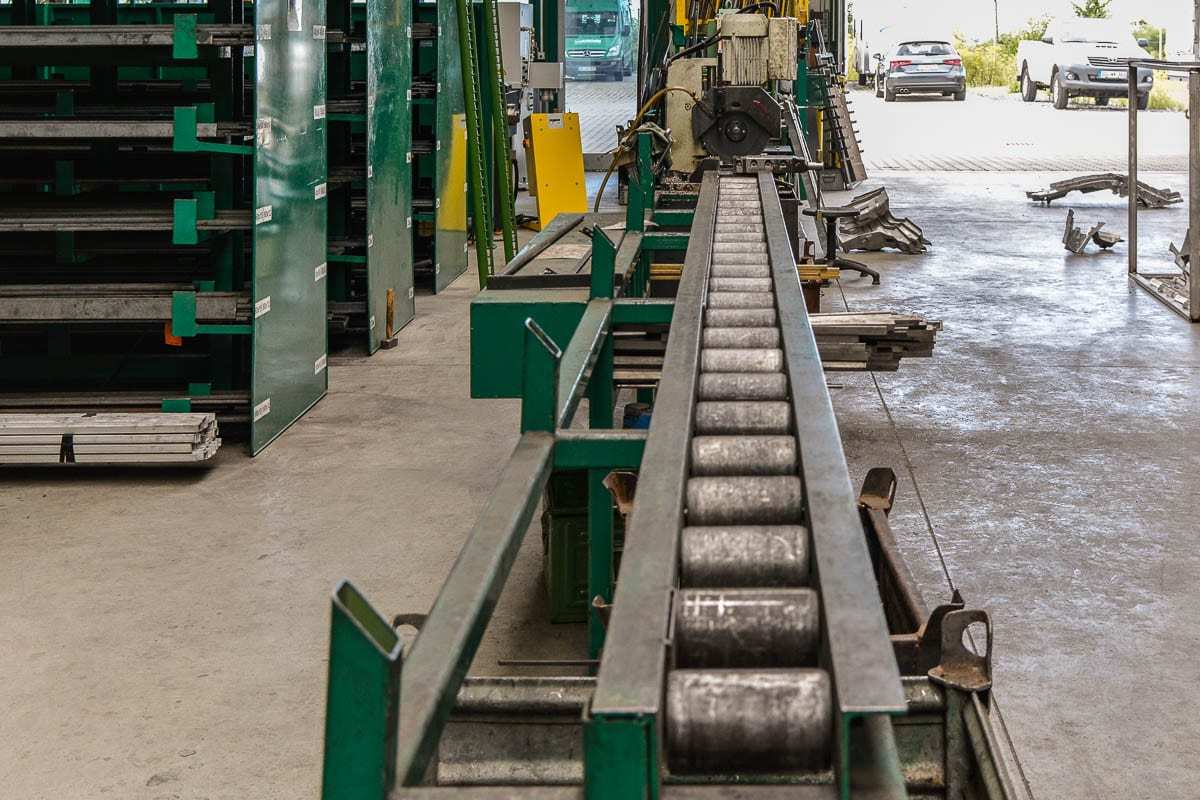
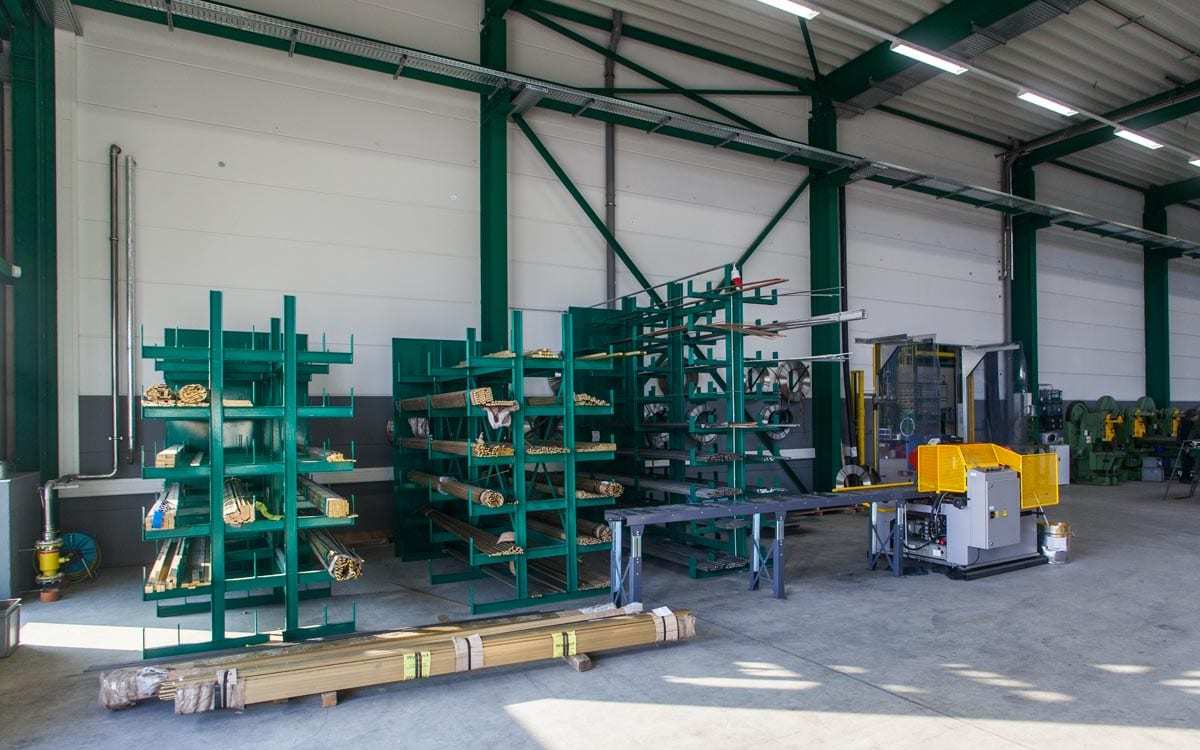
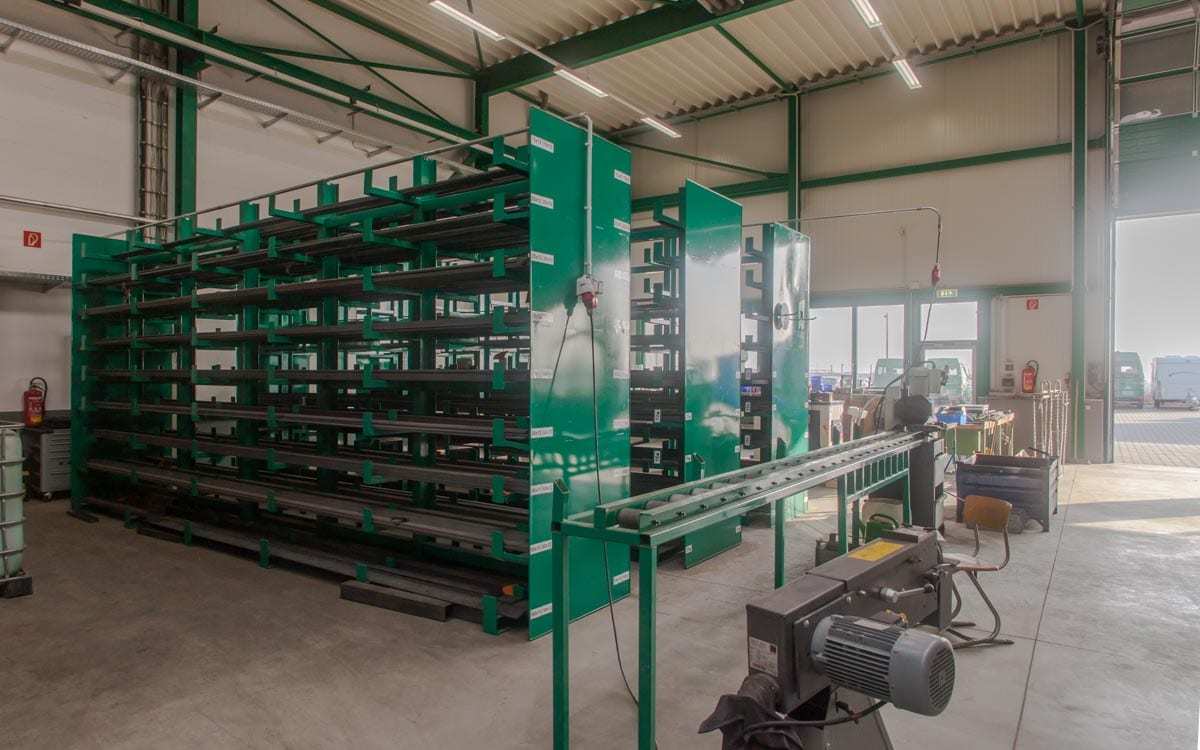
Halle 3
Bauteile Vorfertigung
Ein Großteil technologischer Innovationen zur Metall- und Kunststoffbearbeitung befindet sich in derals Bauteil-Vorfertigung deklarierten Maschinenhalle. Hier werden alle für den Apparate- und Gestellbau benötigten Teile nach Vorgaben produziert und so reibungslos in einem weiteren Prozess der Endmontage zugeführt.
Auf ca. 3000 qm Fläche befindet sich ein moderner CNC-Maschinenpark mit Bohr-/Frästechnik, Wasserstrahlschneid-Technik und mehreren Drahtbiegezentren. Auch eine komplette Blech-Bearbeitungsstraße mit Kantbank, Tafelscheren und Abkantpressen findet hier Platz. Das große am Eingang der Halle gelegene Materiallager erweckt den Eindruck, als ob eine autarke Produktion über Monate möglich sei.
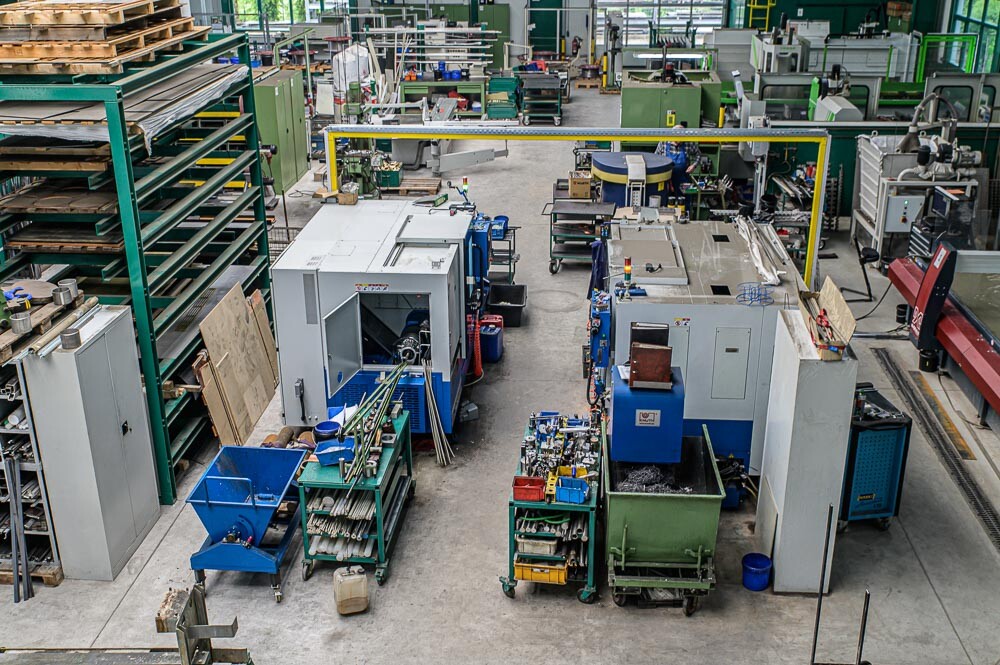
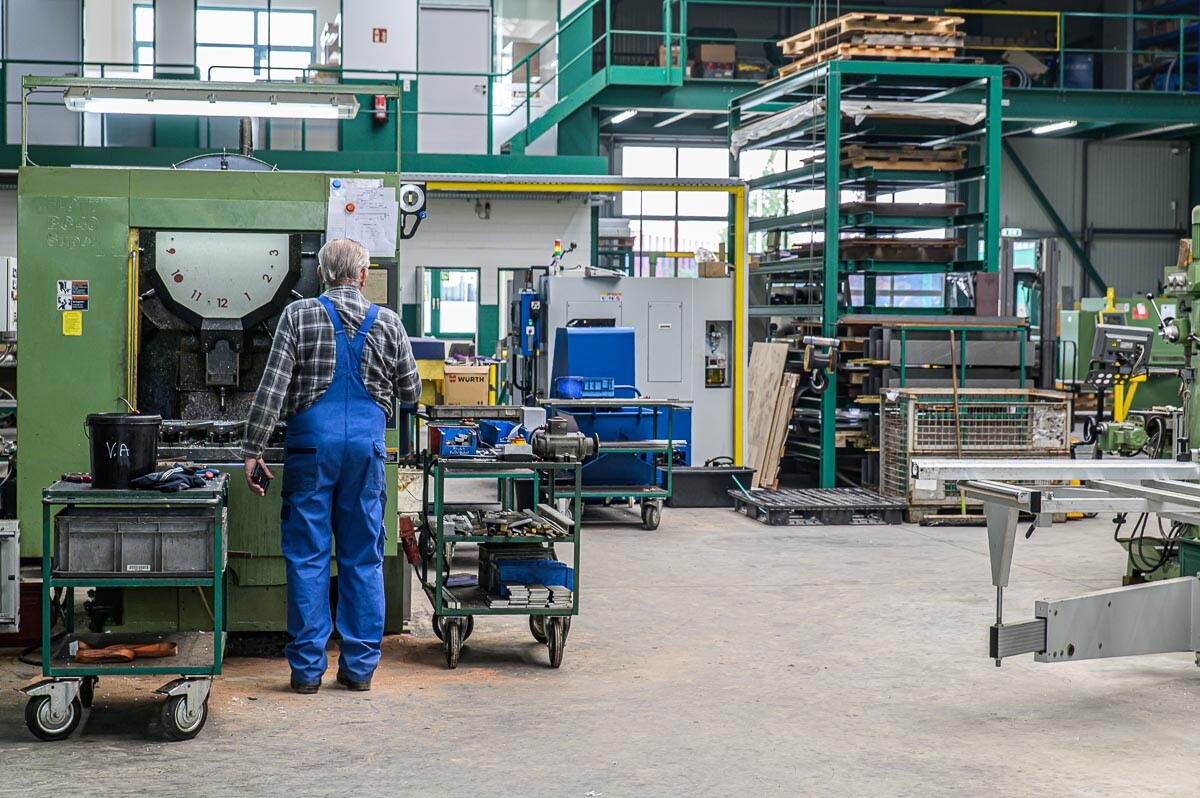
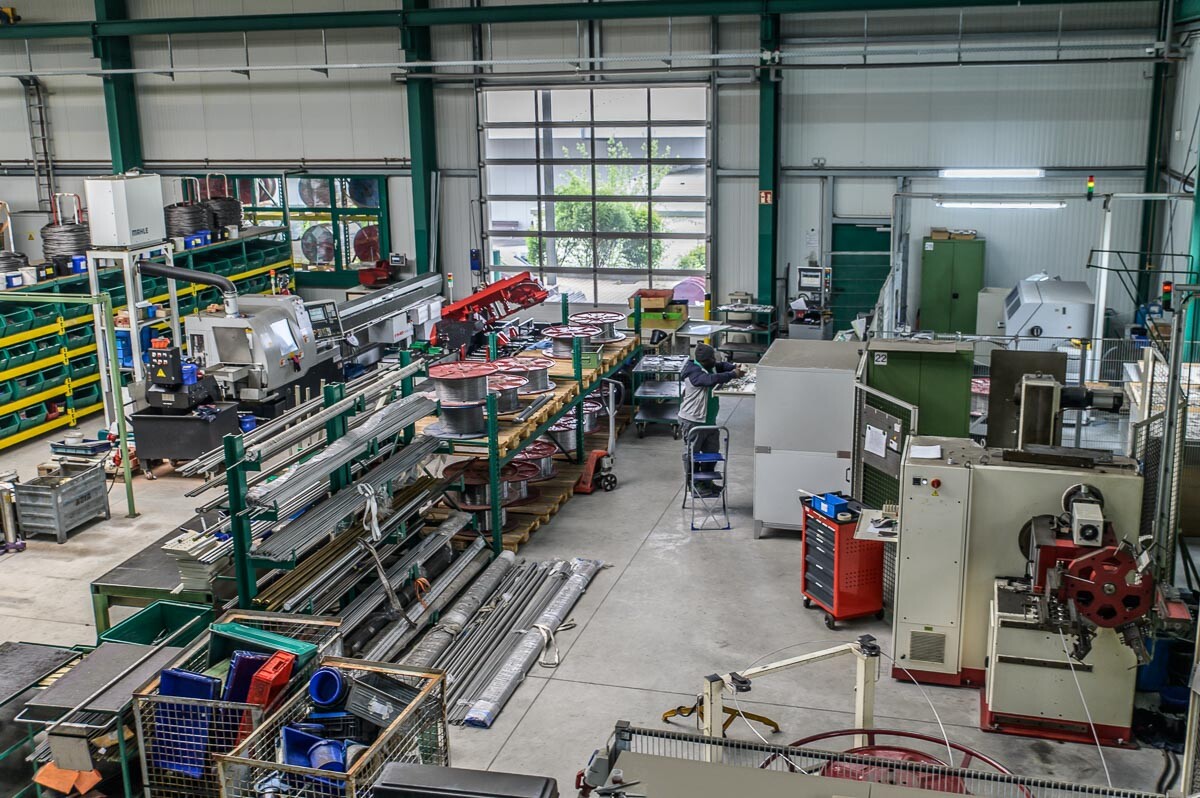
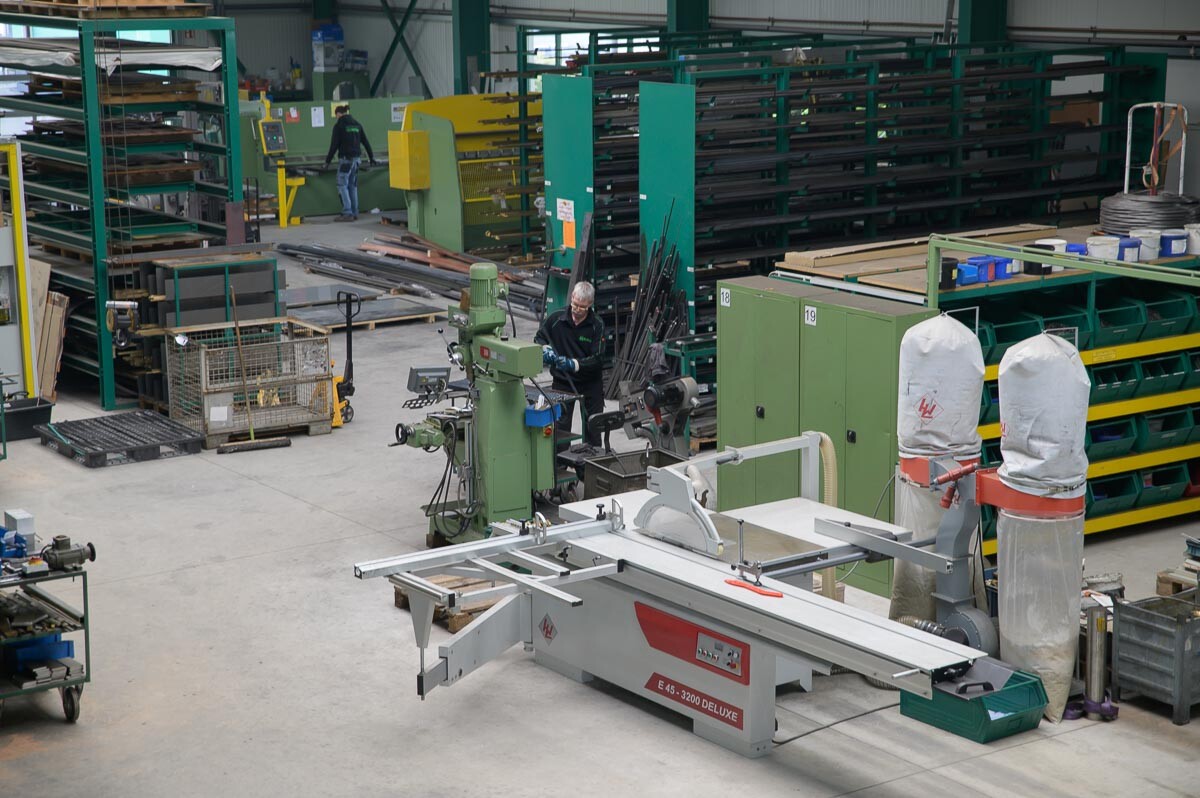
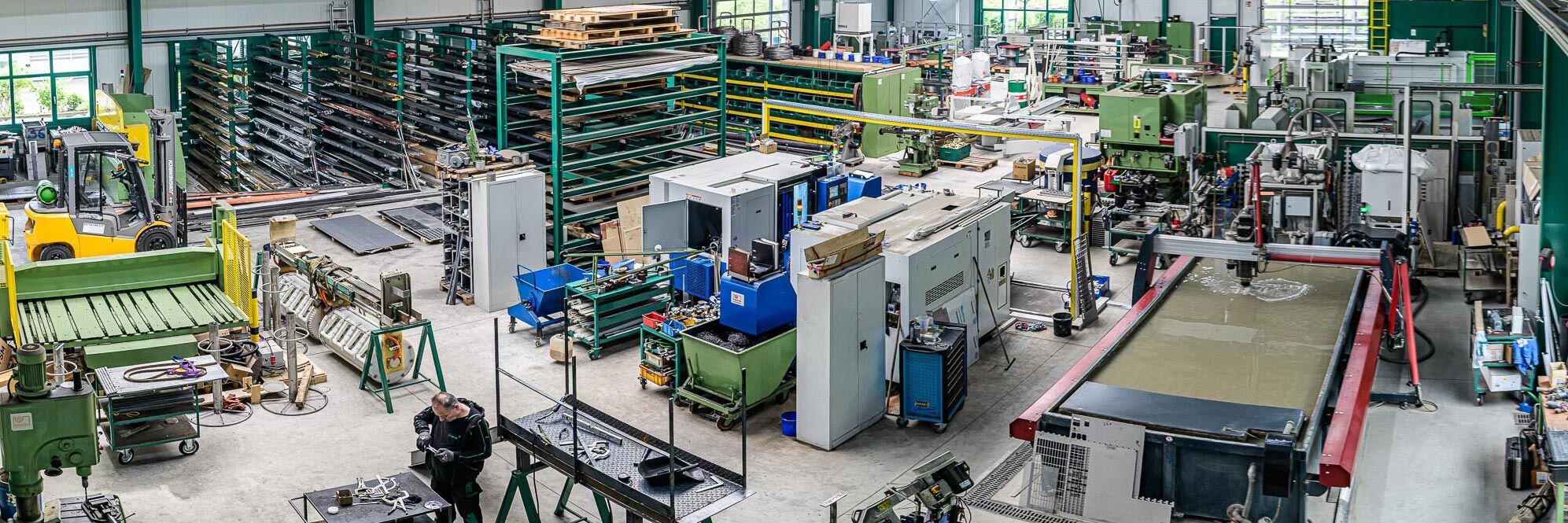
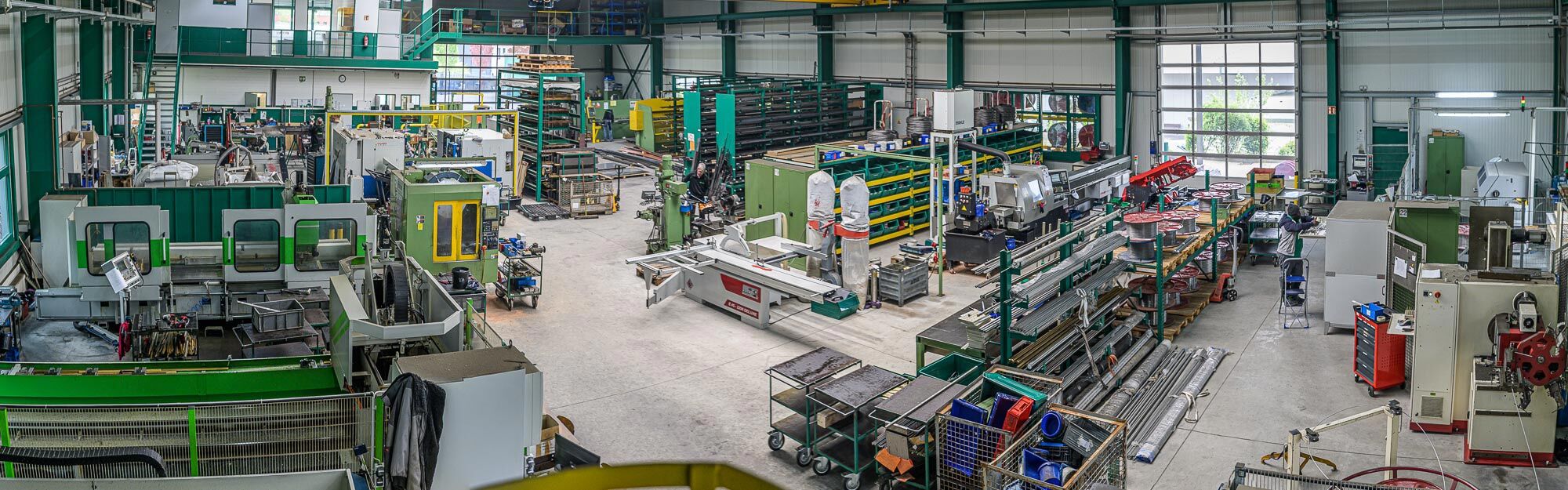
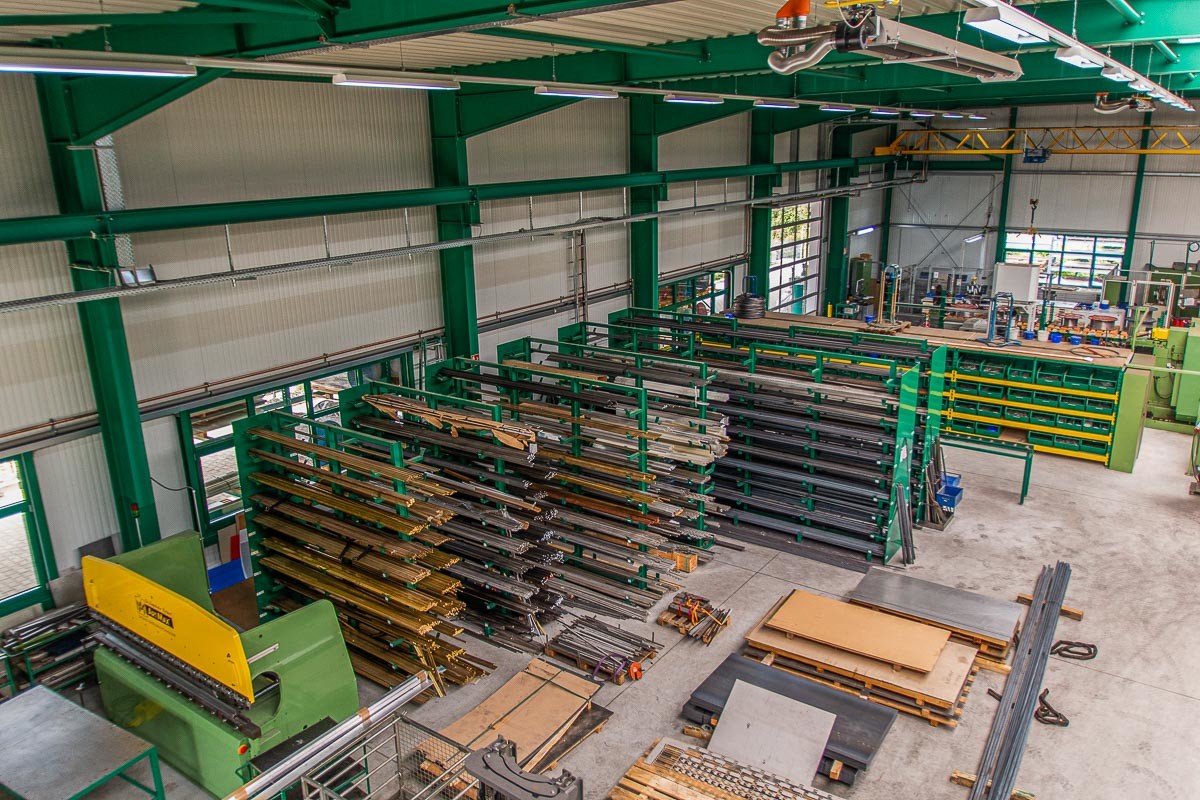
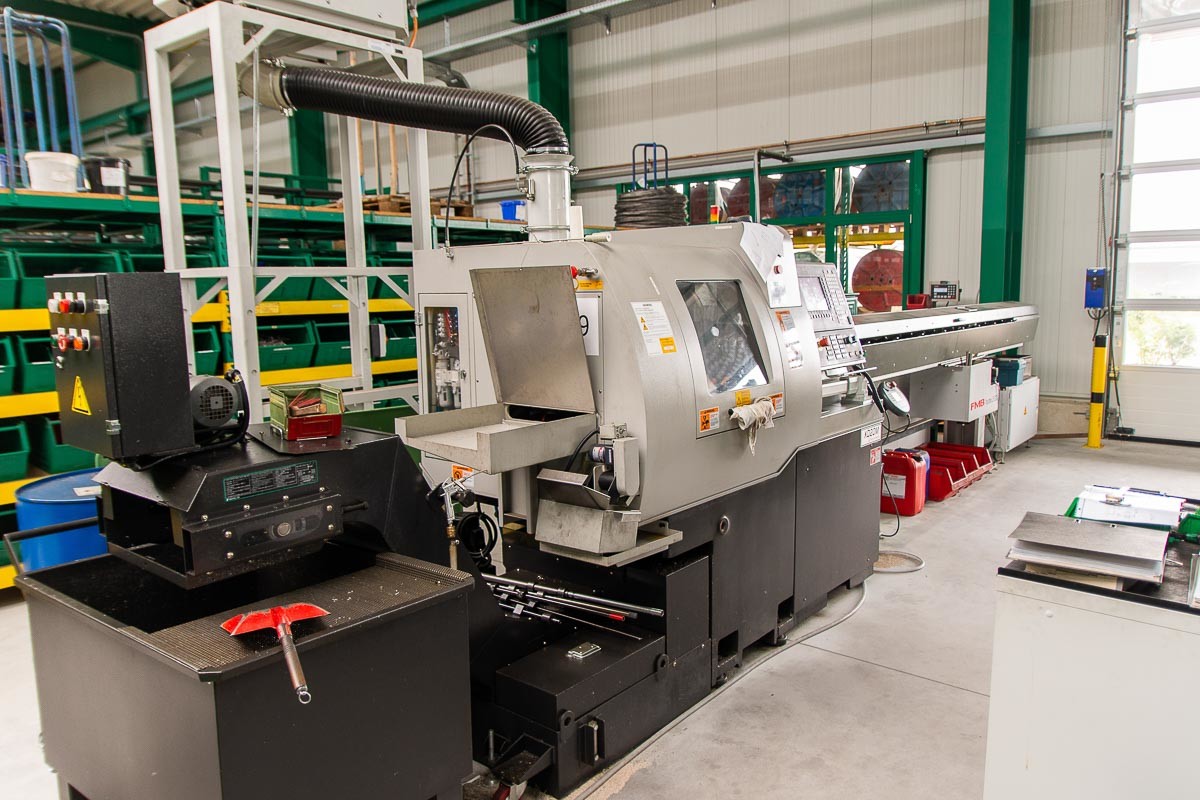
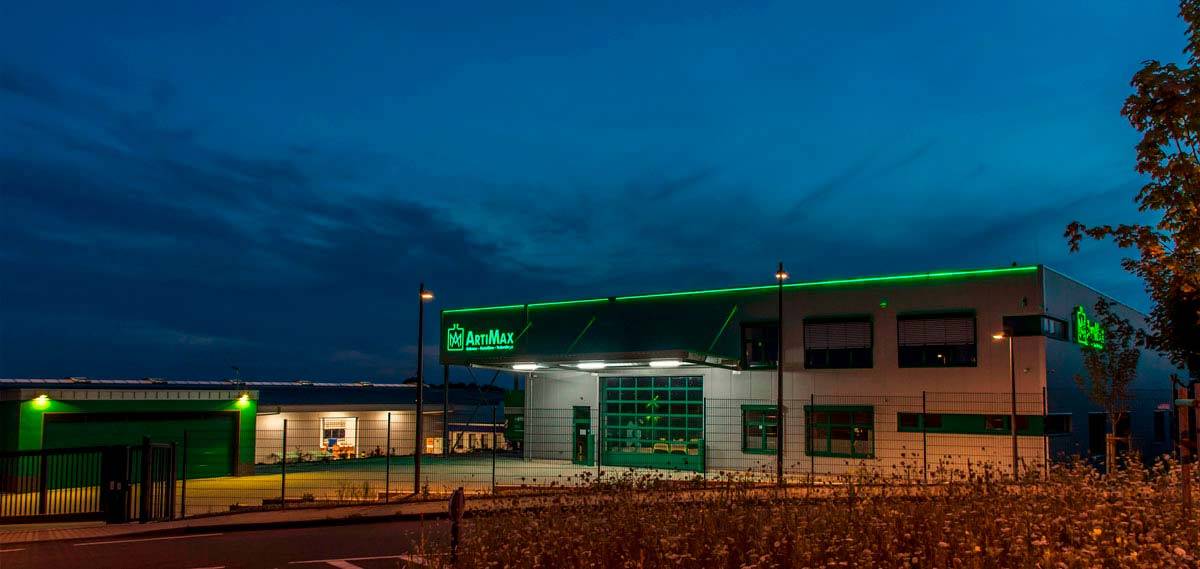
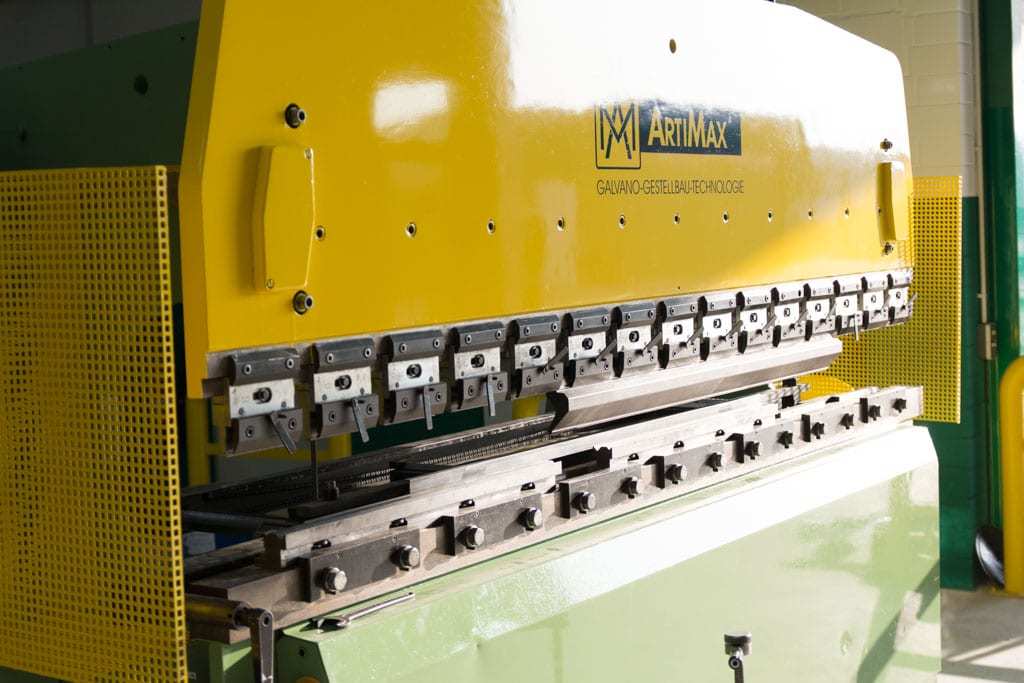
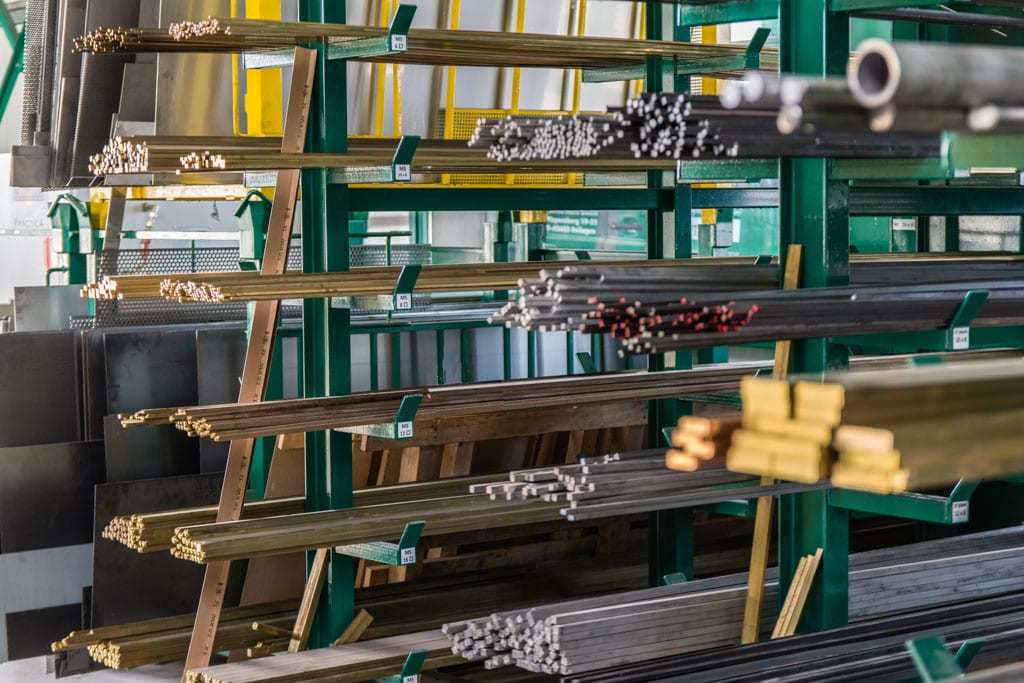
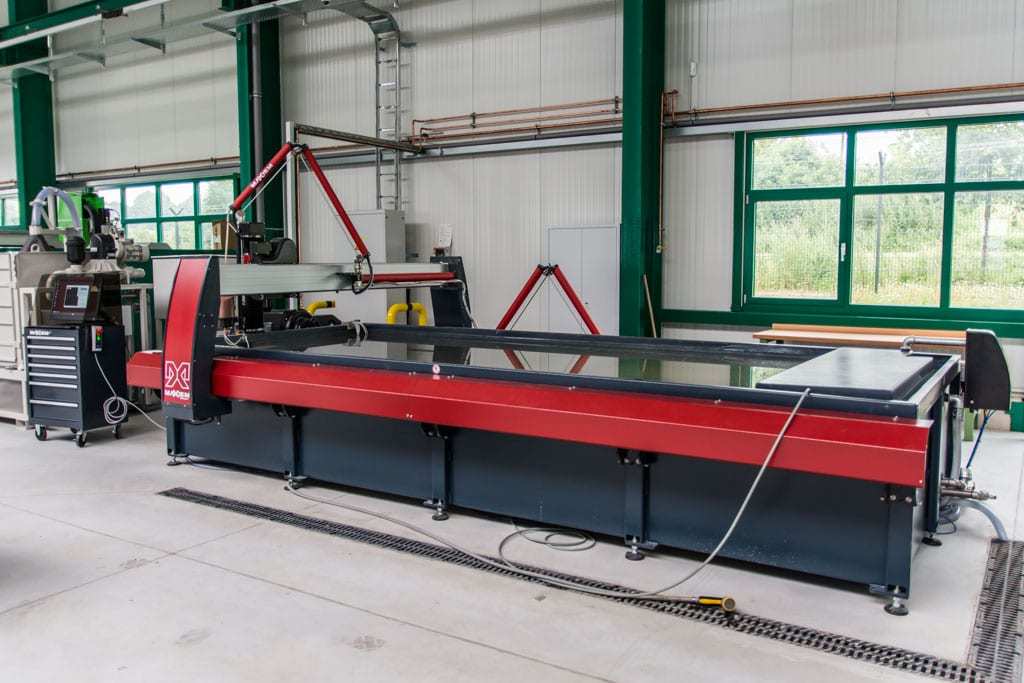
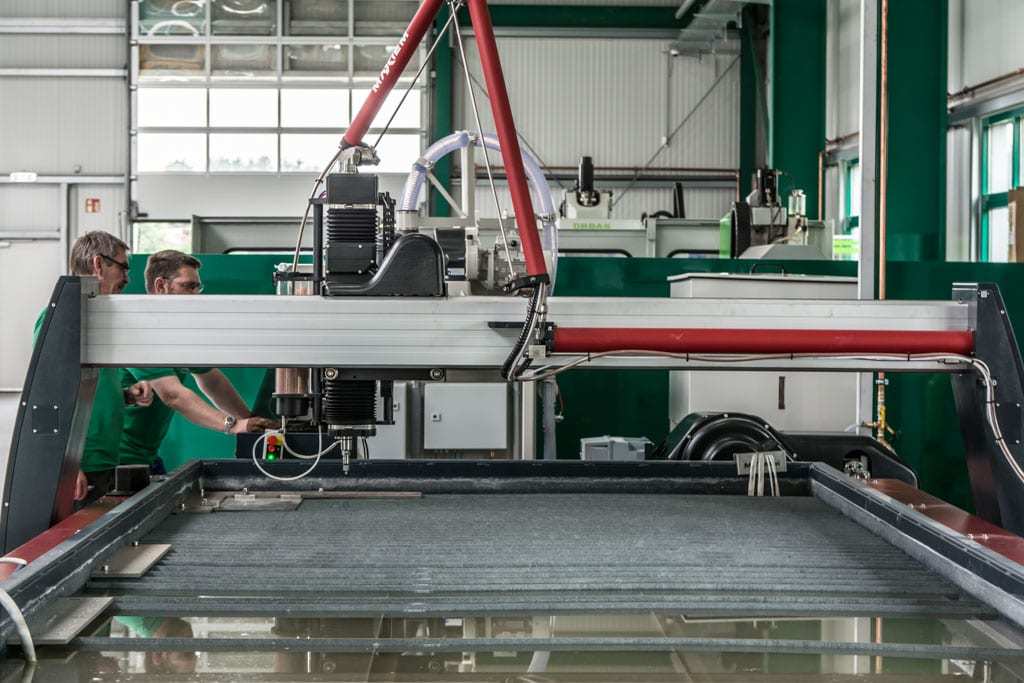
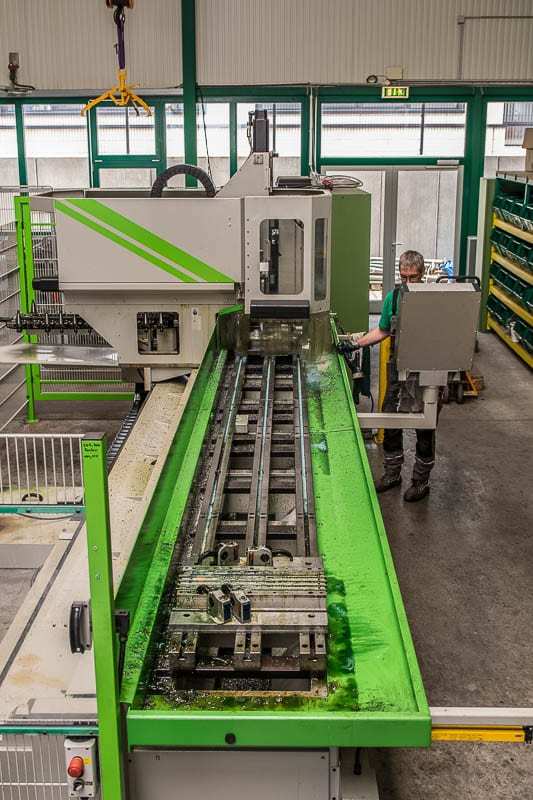
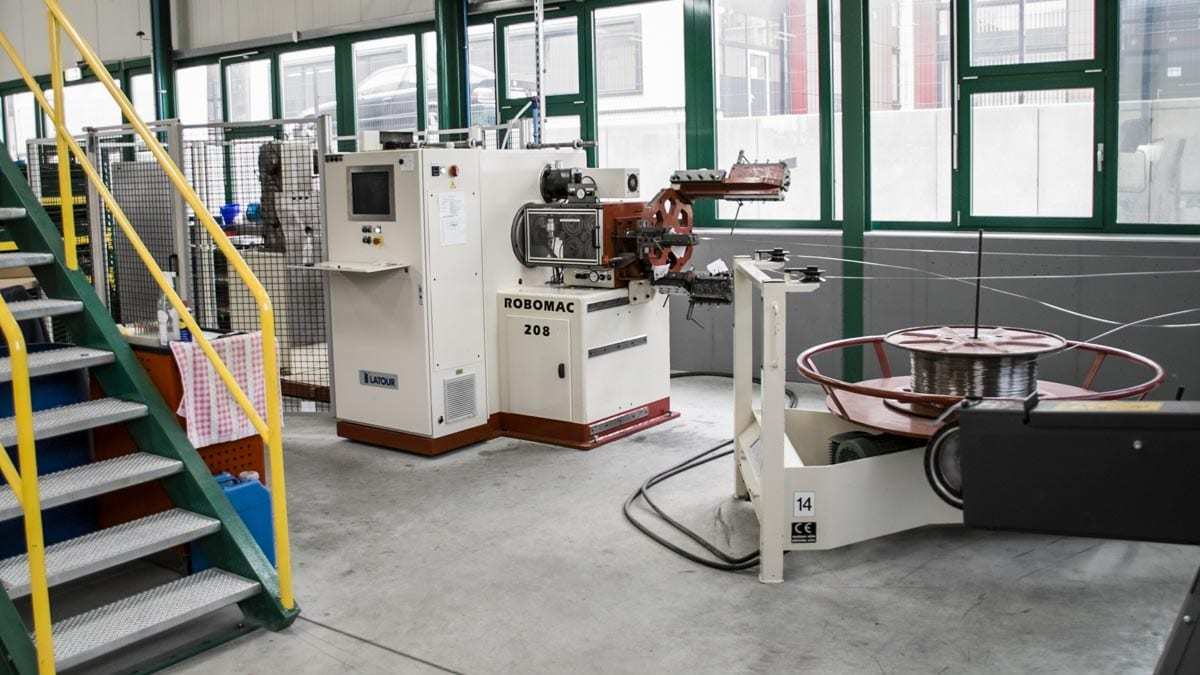
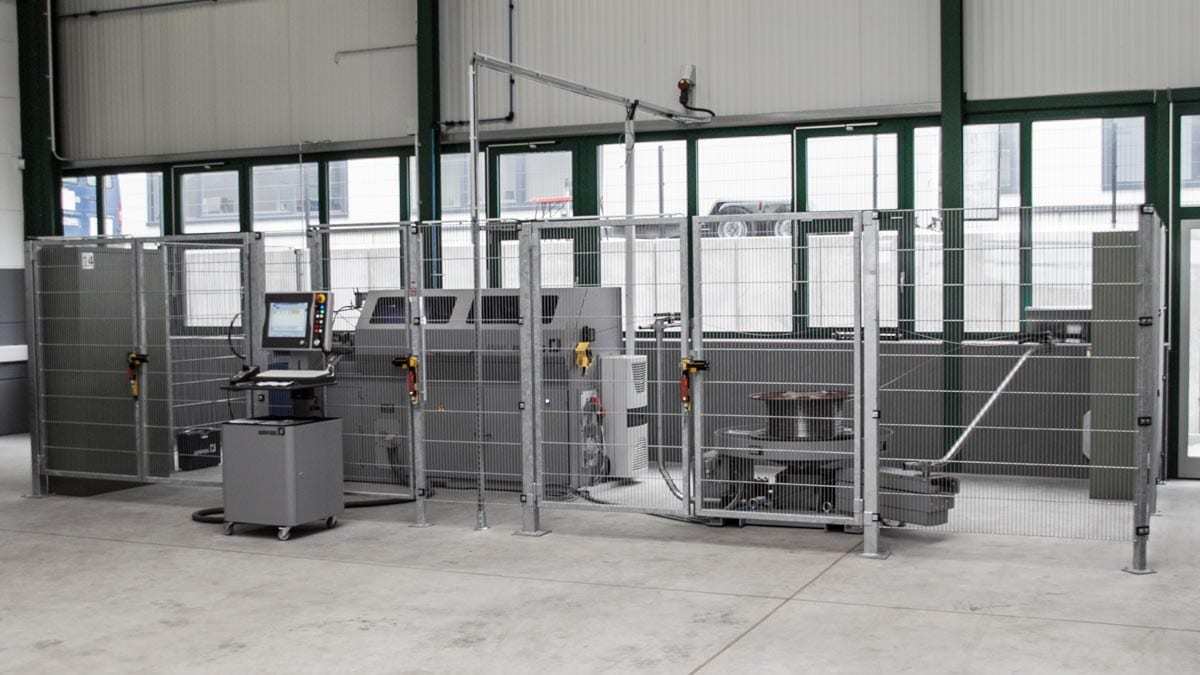
Halle 4
Beschichtung 3.0 – Seminarraum – Arbeitssicherheit – Qualitätssicherung
Im neu errichteten Nebengebäude wurde im Frühling 2021 die europaweit größte Beschichtungsanlage für Galvanik-Gestelle in Betrieb genommen. Gleichzeitig beansprucht sie die modernste Anlage zu sein, mit nach heutigem Stand federführender Filtertechnik und Wärmerückgewinnung, welche nachhaltig in die Energiebilanz des Unternehmens einfließt.
Durch drei unterschiedlich große verschiebbare Becken ist die Alfred Marx GmbH in der Lage,den Kunden verschiedene Arten von Beschichtungen anzubieten und zukünftige, neuartige Gestell-Beschichtungen nach Marktlage zu testen und zu entwickeln. Die Anlage ist eine komplette Eigenentwicklung der Alfred Marx GmbH, es gab keine Vorbilder, aber eine Vision von Herrn Marx. Allein die Kosten für die neue Beschichtungsanlage gehen in die Millionen.
Ein abgeteilter Bereich ist für das Abisolieren und die Endkontrolle der beschichteten Galvano-Gestelle reserviert. Außerdem können die auslieferungsfähigen Gestelle dort bis zum Abtransport zum Kunden gelagert werden.
Zwischen den Werkshallen erstreckt sich der Logistik-Bereich, in dem zeitgleich Transporter und LKWs mit Gabelstaplern wetterunabhängig be- und entladen werden können.
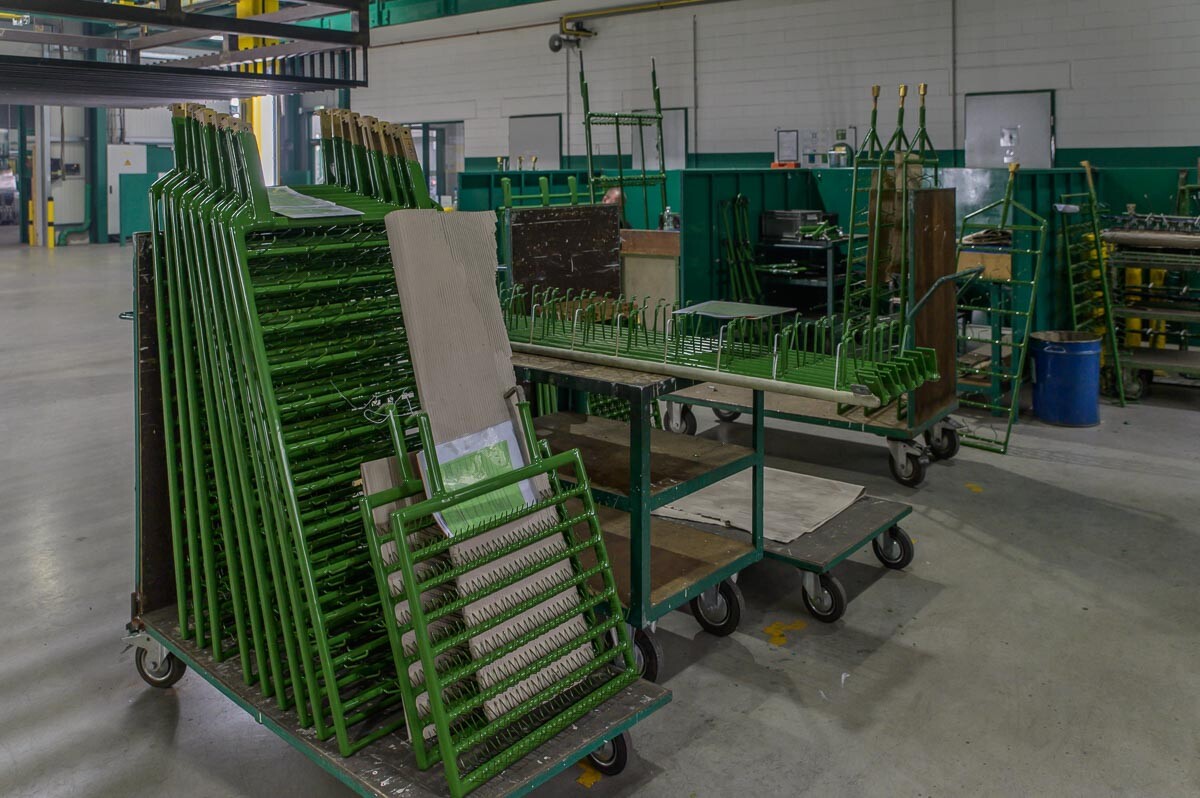
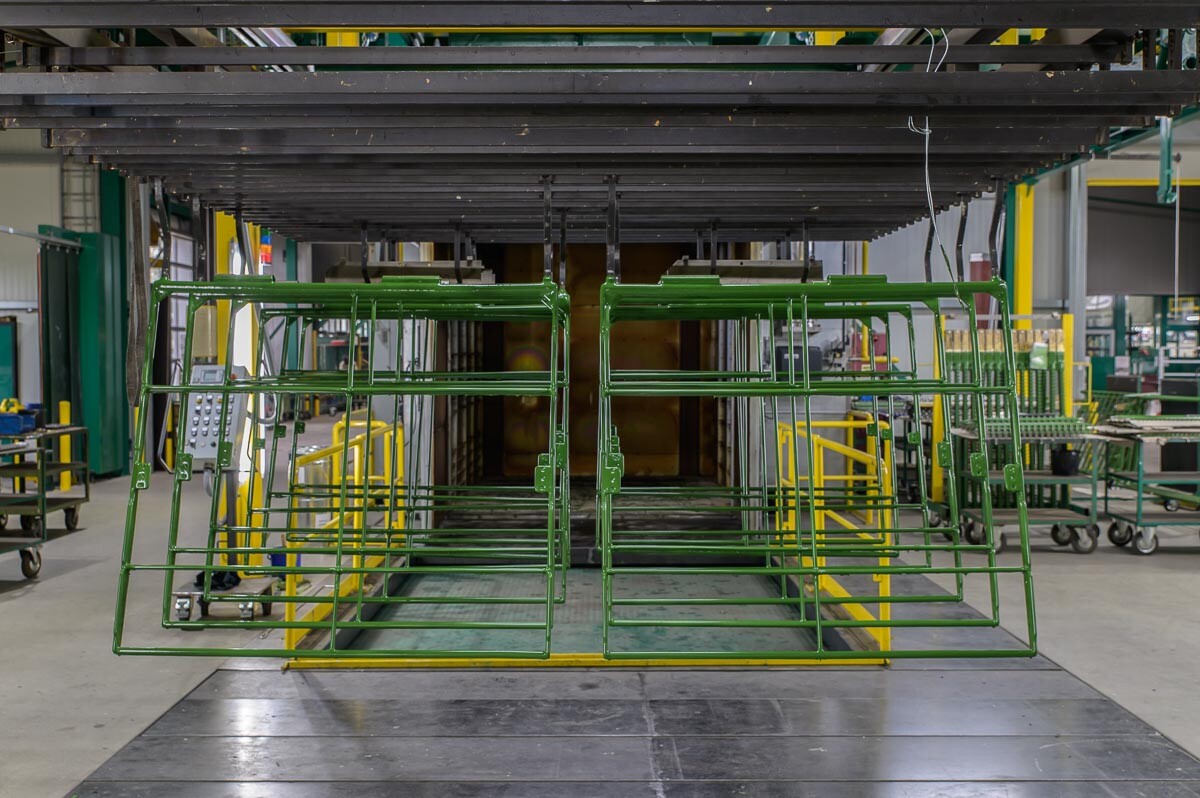
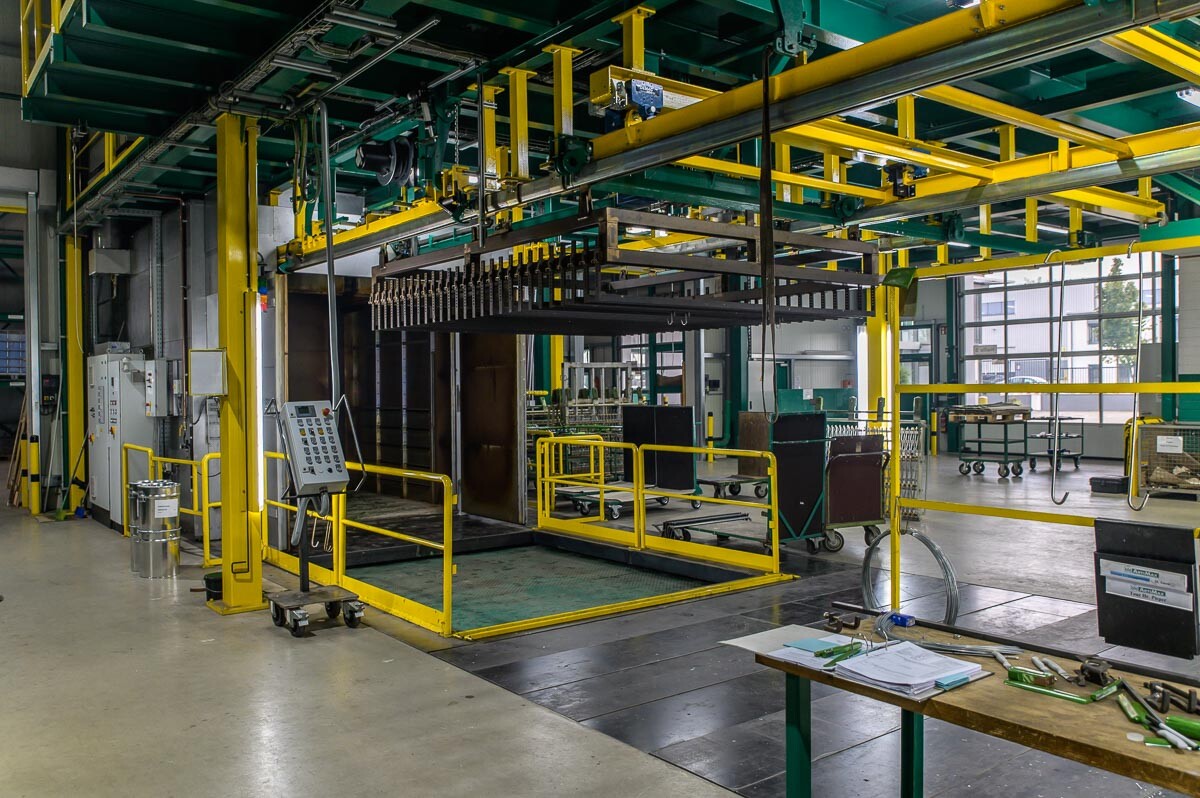
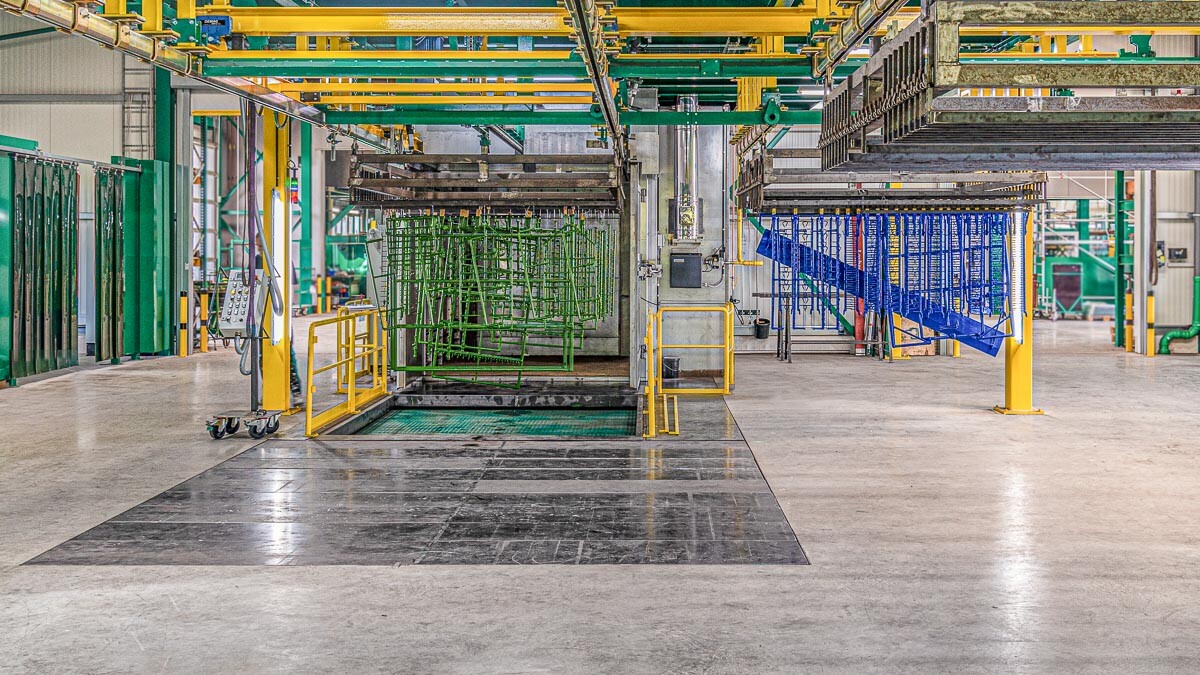
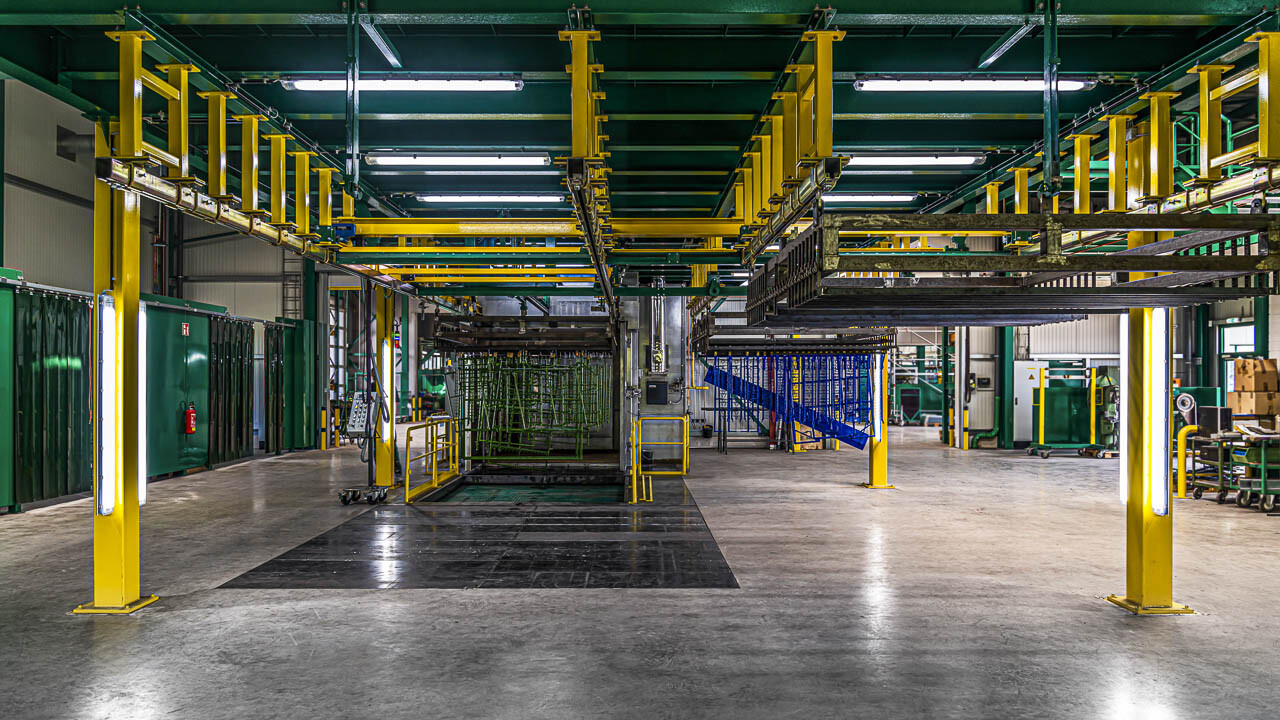
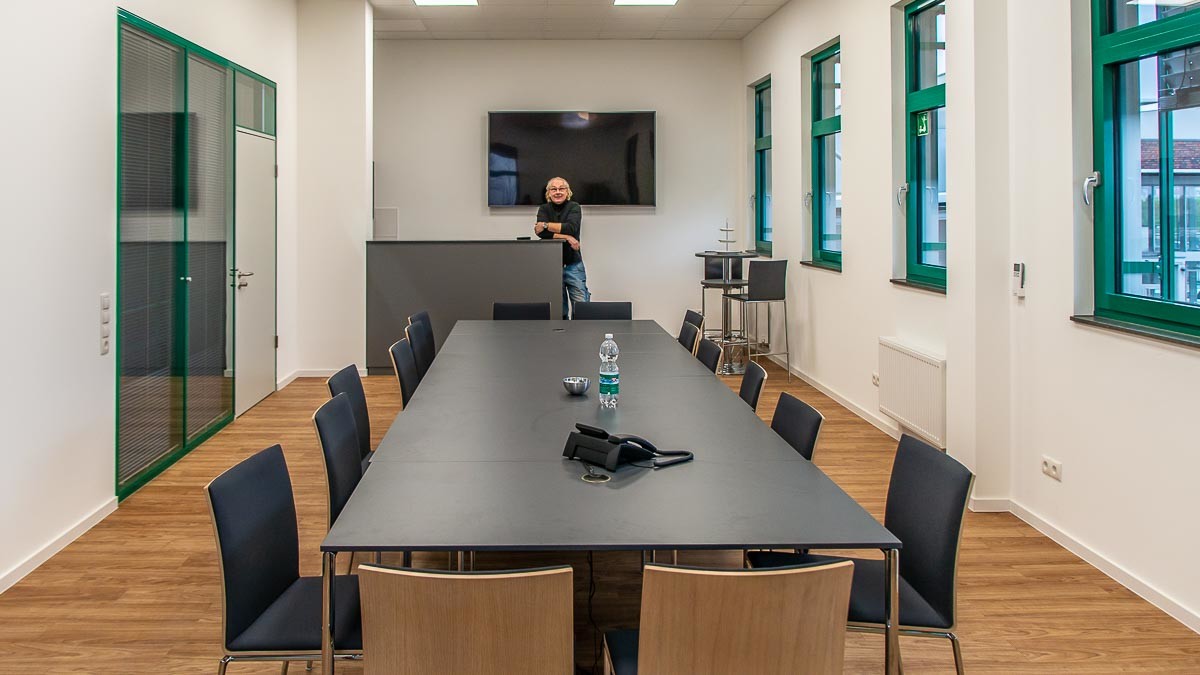
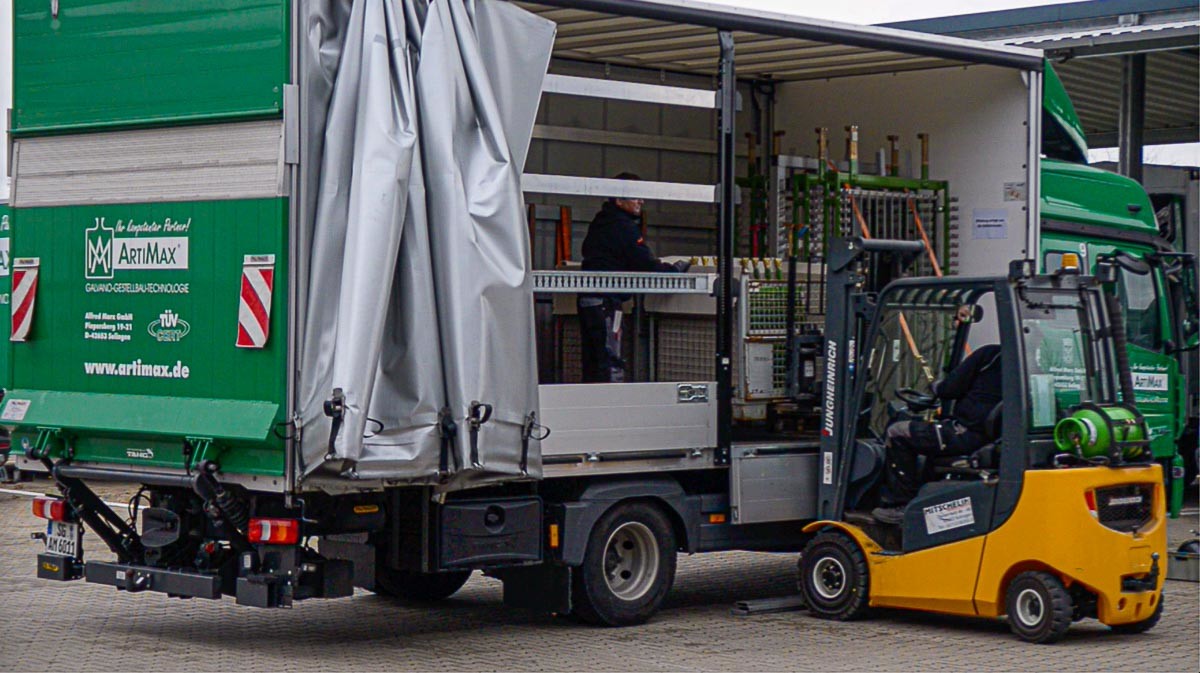
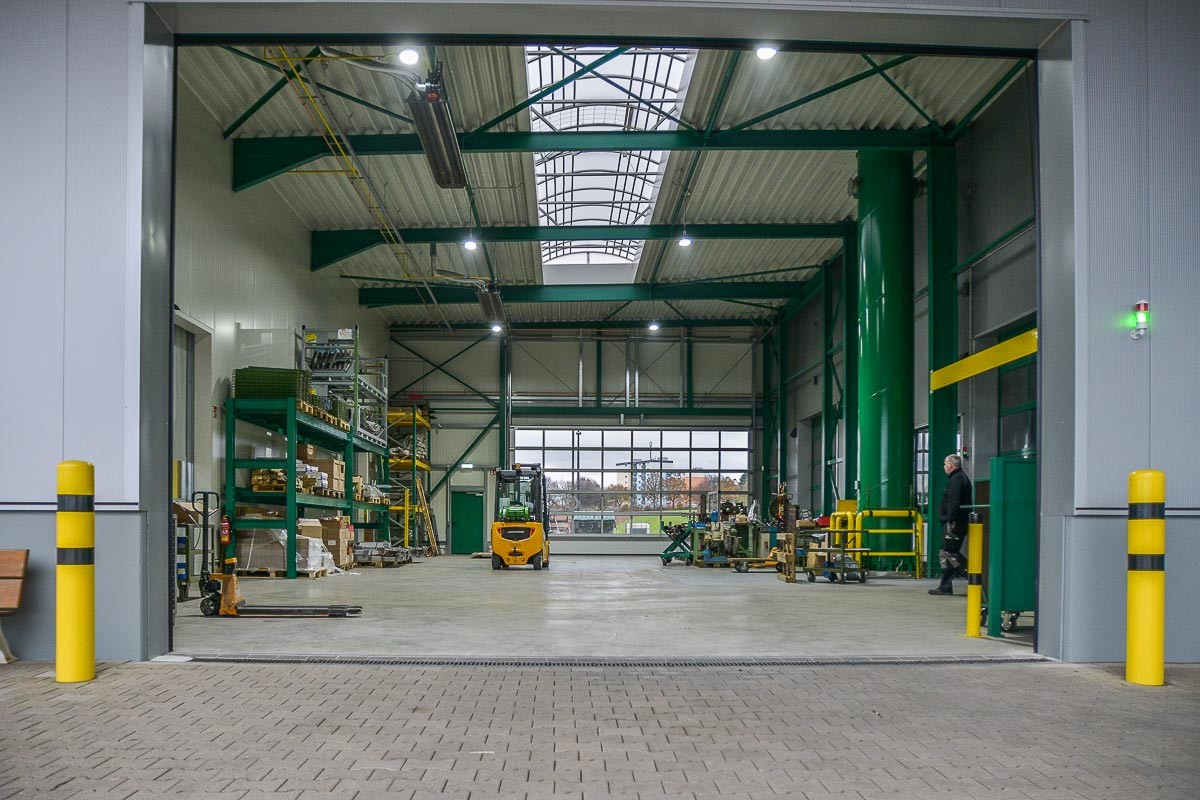


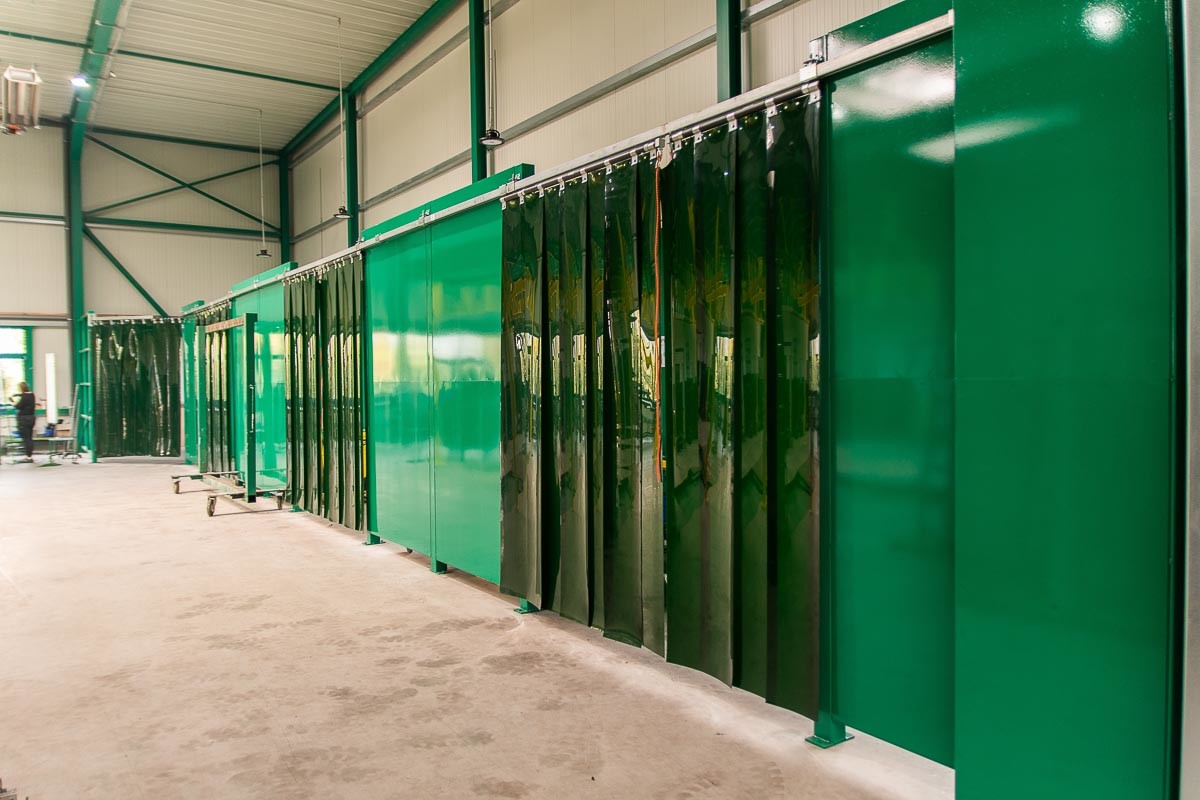
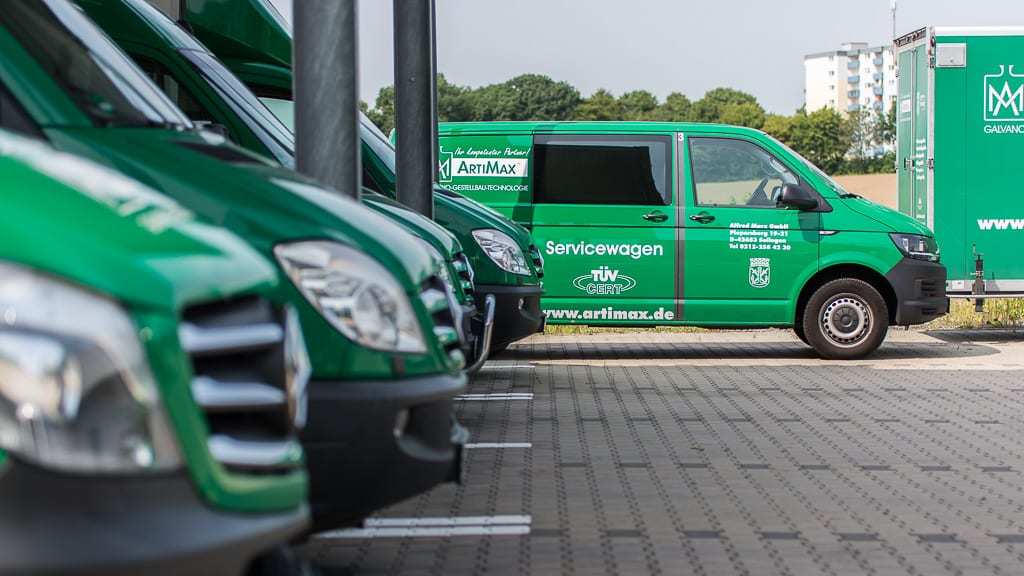
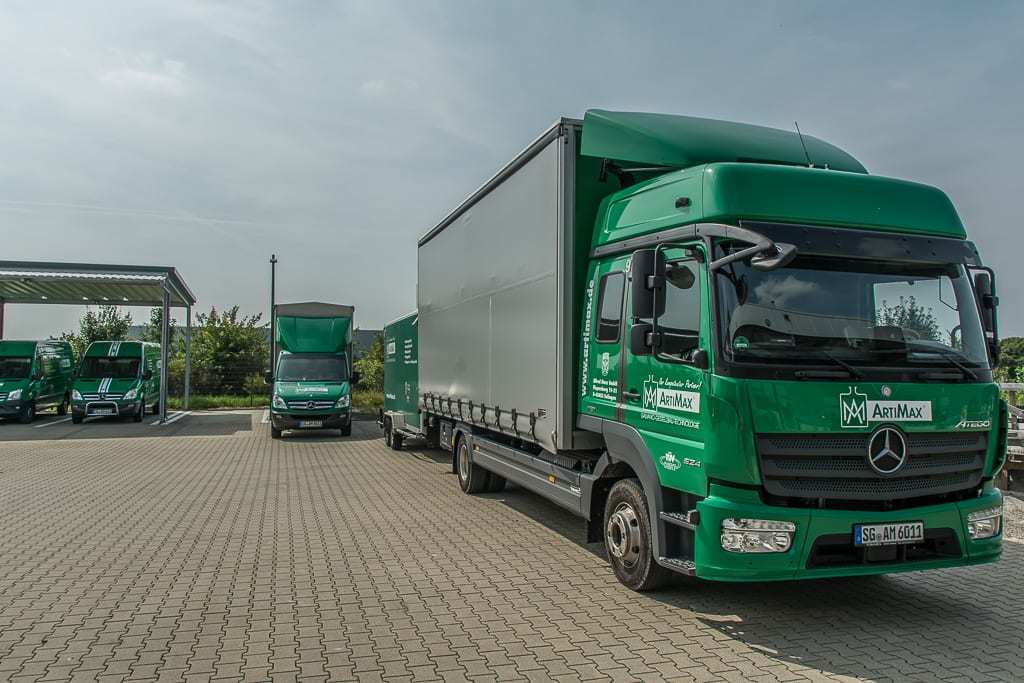
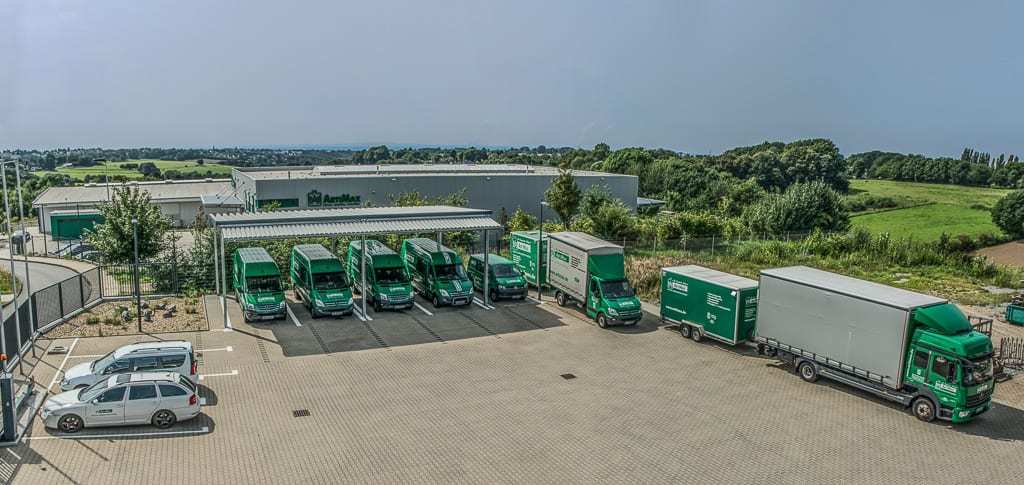